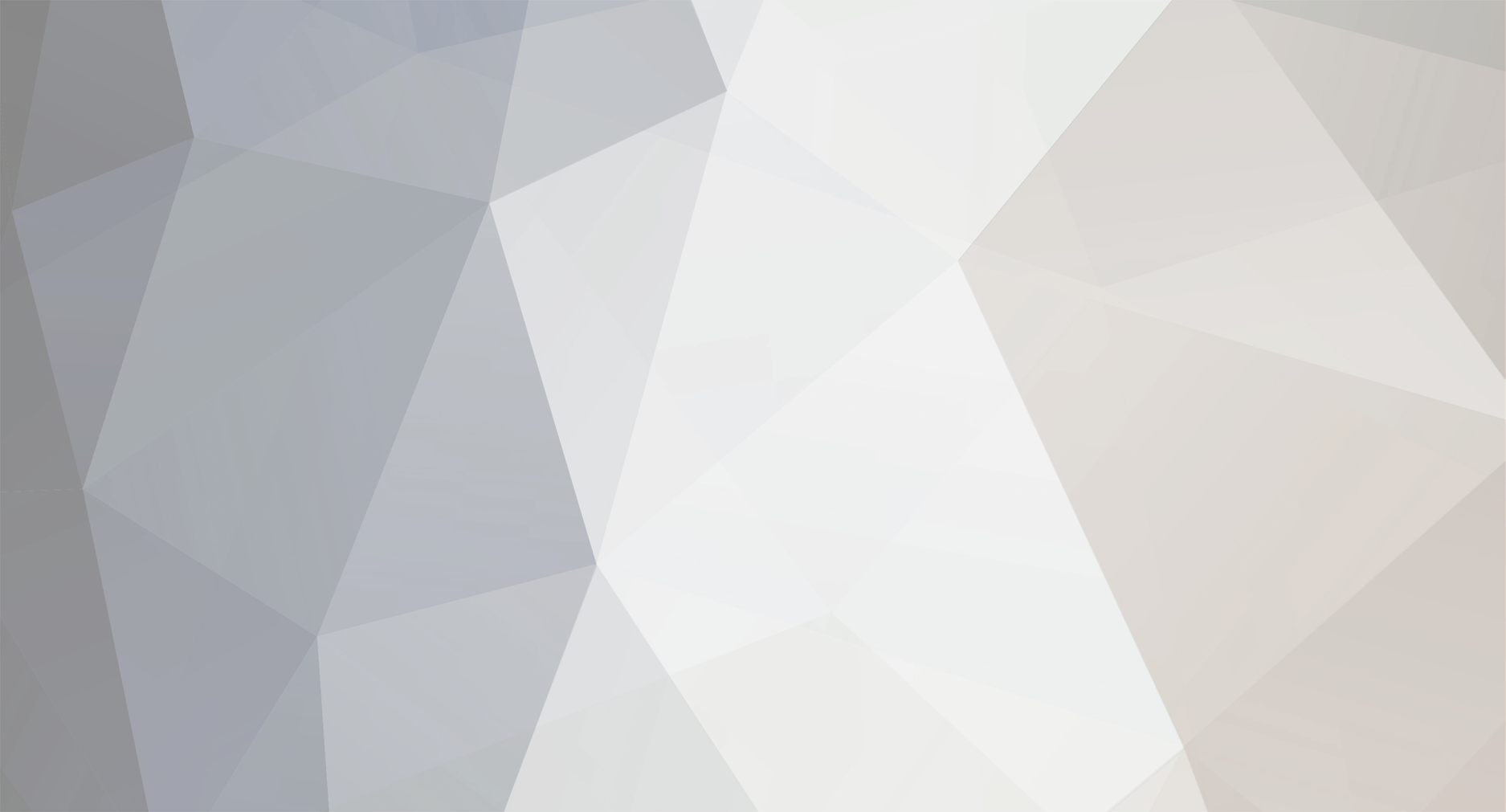
JimL
High Rollers-
Posts
641 -
Joined
-
Last visited
Content Type
Profiles
Forums
Events
Everything posted by JimL
-
If you don't mind used, the Shure E4C runs about $100 on ebay. It got some good reviews at the time, even made Stereophile Class B IIRC. I bought a pair years ago and it's still working, although I don't use them that often.
-
Considering that you're only .067% off, I'd say you're close enough
-
On another subject, I bought a normal bias jack off of ebay from this seller in Estonia: http://www.ebay.com/itm/Stax-Headphones-Kopfhorer-Earspeaker-Normal-Bias-Socket-Jack-Chassis-Panel-Mount-/181879564971?hash=item2a58ddeaab They are delrin, the fit is a bit snug but after pushing the back end of a drill bit into them a couple times I was able to push a normal bias Stax plug into and out of them with just a bit more force than with the HeadAmp jacks. They seem like a good bet if you're building an amp with normal bias, since Justin (HeadAmp) isn't selling normal bias jacks any more. He also sells pro bias jacks. On the upside they're less expensive, on the downside there are striations (machining marks?) across the front, they are delrin rather than teflon, they are black (or very dark gray) and the HeadAmp jacks just look nicer IMHO.
-
For my SRX Plus build, the raw PS is up front, the PS regulator in the middle and the attenuator and amp boards are at the back, with the output wiring lightly twisted going to the output sockets. The length of wire does add a few pf capacitance to the output load but it shouldn't be a major problem. My amp measures 3-5 mV broad band noise at the outputs so there's not a lot of PS noise getting into the outputs. Of course, the PS and all my boards are mounted vertically so the output wiring is just skirting the edge of them, which may make a difference.
-
HI, Frank, Thanks for your comments. I am planning to hold off on discussing my shunt regulator until the second part of the article comes out, probably in mid-Nov. It's not anything special, as I posted earlier it is mostly a combination of circuits that John Broskie has already posted on TubeCAD, with a few refinements of my own. It does use polyprop caps after the regulator section, but I don't know if it really makes that much of a difference. For my phono preamp and line stage I used polyprop caps (phono) and polyprop in oil caps (line) closest to the active circuits and electrolytic caps upstream.
-
I looked at that thread - they have some good info on filament supplies, but I think the curve shown in post #27 is wrong. I base this on an article "Extending Tube Life" by Charles King in Glass Audio Vol1, No.2, 1989. He referenced an earlier article from Audio Dimensions, a tube audio company that was around in the 80s. They showed the same graph that is in post #27 (which is also in Tremaine's Audio Cyclopedia), but then they report data from a study done by GE. GE doesn't have a very good reputation in high end audio, but back in the 50s and 60s it was the 2nd or 3rd largest manufacturer of vacuum tubes in the US. Remember that the biggest consumer tube market back in the 50s and early 60s was the home TV market, so there was a definite interest in improving tube reliability since consumers would get upset if their TVs broke down - none of the modern high end "well our equipment is like a Ferrari, it's state of the art designed at the ragged edge so you have to expect problems" crap. According to the GE study, increasing the filament voltage to 7.5 volts (or a 5670 tube with nominal 6.43 volt filaments, significantly decreased tube life, but decreasing filament voltage to 5.04 volts (80% of nominal) both increased tube life and decreased variation in transconductance over a 5000 hour test period, compared to running the tube at its nominal filament voltage. Although this was done specifically with a 5670 tube, but the results were thought to be generalizable. This contradicts the plot of tube life vs. heater voltage in post 27. However there is more data to support the GE study. Eimac, a manufacturer of RF power tubes, published a report on prolonging tube life which recommended that tubes be run at nominal voltage for a couple hundred hours to burn them in, then gradually lower the filament voltage until emission dropped by 2%, and then turn the voltage back up until the emission was within 1% the original. Of course this requires a RF transmitter with adjustable filament voltages, but the final voltage for long term use was a few percent below nominal for best tube life (I found this article with a Google search for filament voltage and tube life). David Berning's equipment, which uses 12AX7, 12AT7 and 6SN7 tubes in preamps and amps, also uses lower filament voltages (typically 5.7V for 6.3V tubes) and he routinely claims 10,000 to 20,000 hour tube life - his company has been around since the early 1980s, and I've not seen or heard anything to indicate that his equipment needs tube replacements more frequently than his claims would suggest. Note that these are the same tube types used in the SRX Plus so the results should be directly applicable. I think, therefore, that there is good evidence that dropping the filament voltage by 5-10% will improve tube reliability and service life. It may be that the curve shown in post #27 and the Audio Cyclopedia are correct if you are running a tube at or near its maximum, but good design for reliability and tube life dictates that tubes should be run significantly below the maximum.
-
One other thing which I forgot to mention above. I run AC filament supplies, but I also add small value resistors in series (i.e. 0.2-0.5 ohms) to lower the voltage across the filaments to 5.7-6.0V RMS rather than the 6.3V design center. This results in a negligible decrease in tube emission but a significant increase in filament life. Those of you who are old enough to remember tube TVs, which were ubiquitous in the 50s to early 60s, will remember that they would run day in and day out for years before needing any tubes replaced, and this is one of the ways they used to accomplish that. The other way is by designing conservatively to use the tubes well below their voltage, current and power limits, which is what I've done in the SRX Plus. I estimate that tube life should be in the 10-20,000 hour range with NOS tubes.
-
The publication date for the SRX Plus in AudioXpress has been pushed back a month, to Nov and Dec. The first part covers the amp circuit, which I’ve already discussed, and the second the power supply. In the interim, I thought I would start discussing the power supply. My raw power supply design is a bit different, in some ways a throwback to pre-World War II days. There isn’t really anything new about it, and in fact I used a similar design in a phono preamp project published a decade ago. Nor do I claim it is better or worse than current orthodoxy, but it is different, with both advantages and drawbacks that are worth discussing. Pretty much all the power supplies in Head-Case projects that I have seen are solid state rectifier capacitor input supplies. If you look at the schematic above, you will see that mine is a hybrid rectifier choke input filter supply. The bias supply is a direct steal from Dr. Gilmore - if you're going to steal, steal from the best. Transformer The first thing you may notice is the transformer has a higher secondary voltage than usual, although the ultimate output voltage is +/- 340V or so. This is because a choke input filter outputs a voltage that is close to the RMS voltage of the secondary, as opposed to a capacitor input filter, which outputs a voltage close to the peak voltage of the secondary – the latter is about 1.4x higher than the former. I used a surplus transformer with an electrostatic shield between primary and secondary to minimize the amount of noise and hash coming in through the AC line. The secondaries were specified at 780VCT center tapped/50 mA with two 6.3 volt/1.2 amp filament windings and a 5volt winding, which I used with a voltage doubler to power the HV delay (not shown). A separate 6.3V/1.6 amp transformer was used to power the 6BY5GA dual damper diode rectifier. Unfortunately the AC power line is often contaminated with noise and spikes from appliances turning on and off, light dimmers, etc. The electrostatic shield helps minimize the amount of power line crud that gets into the secondary of the power supply. It is found in transformers from Antek, for example, which a number of Head-Case members have used for their builds, and is routinely found in professional, industrial and medical electronics, but is generally missing in “high end” audio equipment. Rectification Every time a rectifier turns on or off it generates voltage spikes. These spikes produce broad band noise that has to be filtered out. The problem is that the high frequency noise generated is often not well shunted to ground by electrolytic capacitors and so gets passed down the line. The common 1N4007 diodes are among the worst offenders. Soft recovery diodes such as HEXFREDs or Schottky diodes, and tube rectifiers generate less noise, with tube damper diodes as a class generating the least noise. Tube rectifiers also turn on slowly, allowing the filaments of the signal tubes to warm up before the high voltage turns on. Of course tube rectifiers have their downsides: they need a filament supply, they wear out, and they cannot tolerate large input capacitors. Together with their relatively high impedance, this results in significantly less “stiff” power supplies, with DC voltage varying with changing demand. However, since most electrostatic headphone amplifiers are class A, differential and balanced, their current demand is pretty constant so a “soft” power supply isn’t too much of an issue. Since the SRX Plus needs a bipolar high voltage supply, a bridge rectifier is required. Implementing this with tube damper diodes would require 4 diodes and at least 3 filament supplies (the two positive legs of the supply can share a filament supply), which is a significant complication. As I was in an experimental mood when I built the SRX Plus, I used a hybrid rectifier with a 6BY5 dual damper diode tube for the positive legs and soft recovery diodes for the negative legs, and a HV delay and ramp up circuit from K&K Audio with an 11 second delay and a couple seconds ramp-up on the B- side to roughly match the turn on characteristics of the damper diode tube. This was an attempt to get some of the noise and turn on benefits of a tube rectifier while only needing one filament supply. This experiment was partially successful, in that there was a nice delay in HV, however, since the turn-on of the positive and negative halves were not perfectly matched, the amplifier output voltages initially went negative then positive, before drifting down to zero over 30 minutes or so (the drift being due to amp warm-up). While it can be a bit disconcerting watching the voltages moving up and down by a couple hundred volts or so within a few seconds, since the amp is fully differential, the positive and negative outputs tracked each other well, limiting turn on and turn off noises. For those who don’t want to bother with a tube rectifier, a regular solid state bridge rectifier would work. High voltage HEXFRED soft recovery or Shottky diodes would generate less noise than other solid state diodes. Filtering There are two ways of filtering the raw rectified AC, capacitor input filters and choke input filters. Pre WWII, when iron and copper were cheap and capacitors were expensive, choke input filters were the norm. Nowadays when iron is expensive and capacitors are cheap, capacitor input filters are nearly universal. However, there is one significant disadvantage to this topology. With a capacitor input filter, there are large current spikes, because the capacitor only fills up at the peak of the voltage waveform when the input voltage exceeds the voltage already on the capacitor. So during that brief period of time, there is a large current surge to top up the cap. These brief current spikes may peak at many amps even though the average current may be only a fraction of an amp. The late Allen Wright likened these spikes to whacking the power supply with a ball peen hammer 100-120 times a second. Those spikes produce lots of broad-band noise. Soft recovery diodes do little to reduce this source of noise as the current spike is largely independent of the type of diode it is running through. Tube rectifiers produce less of this, because their relatively their high impedance limits the amount of peak current during the spike. Thus, the strength of solid state rectifiers – their low forward impedance and ability to pass large currents to top up large capacitors, is also their weakness from the viewpoint of noise generation. Choke input filters avoid this source of noise because the current flows throughout the whole cycle, assuming a proper value choke, and so are inherently quieter. I feel it is preferably to generate less noise to begin with rather than trying to filter it out afterwards – an ounce of prevention, etc. Choke input filters also match well with tube rectifiers, which cannot tolerate a large capacitor input filter – most tube rectifiers are specified to work with input capacitors of 20-50 µf at most. The inductance of a choke acts like an electrical form of inertia to keep the current flowing during the downside of the voltage cycle to smooth the current flow. Finally, choke/capacitor filters do a better job of removing residual AC line crud (12 dB/octave) than RC filters (6 dB/octave). The output of a choke looks more like a simple sinusoid - easy for the filter caps to deal with. This also makes the job of the power supply regulator much easier. Even the simplest regulators have relatively high rejection ratios for hum and other low frequency garbage. Where they tend to have trouble is at high and ultrasonic frequencies where the rejection ratio diminishes. Note that these benefits only occur if the input section is a choke. If you use a capacitor input filter, you still have the large current spikes. A choke section down the line will help with noise filtering, but real world chokes have shunt capacitance that can still allow some high frequency noise to pass through. With choke input filters, there is no derating of the transformer needed. A transformer rated at 50 mA AC will easily supply 40-some mA DC current without strain with a choke input filter. With a full wave bridge cap input filter, the minimum AC rated current is 1.8 x the desired DC current. I used two LC sections each on the B+ and B- supplies – that’s four chokes and four capacitors, which is probably overkill. But the result is a nice, quiet raw power supply. In fact I used a single ended version of this with damper diodes, 20H primary choke and electrolytic caps on both sections as the raw power supply for my tube phono preamplifier, which has a passive power supply (if you’re interested, it was published in AudioXpress 1/04 and 2/04). If choke input filters are so great, why doesn’t everyone use them? Well, chokes are expensive, heavy, and bulky. My tube phono and line preamps and SRX headphone amp, which all have choke filtered supplies, weigh around 40 lbs each, and the power supplies occupy at least 2-3 times as much space as the active electronics – you cannot build a mini-SRX, or mini anything else, for that matter, using a choke filter power supply. Forget it if you want a small bedside table amp. Also, you need a higher output voltage from the transformer – the RMS voltage has to be higher than the final raw DC voltage. For a high voltage supply, sourcing transformers can be a problem. Antek does have 400 to 500V RMS secondary transformers if you’re willing to go to 400VA, which would be total overkill - not that there’s anything wrong with that. But it is additional buik, weight and expense. The 500V RMS would work for building a choke filter supply for a Blue Hawaii or +/-400 volt KGSSHV or Carbon, with 5-6H chokes, if you’re so inclined to experiment with choke filter supplies – just make sure you’ve got a strong back or a working fork lift. So, a different methodology for your consideration.
-
Here's a link to a picture of the SRD7SB Pro http://stereonomono.blogspot.com/2014_09_01_archive.html
-
Spritzer stars in Innerfidelity Big Sound 2015 video - (but not in person!)
JimL replied to complin's topic in Headphones
Very cool, congrats to Birgir and Dr. Gilmore who also was mentioned. -
Just one caveat. The SRM1 Mk2 was last made in 1995, so they are at least 20 years old, which means at a minimum that their power supply caps are well past their sell-by date and should be replaced with modern equivalents or better.
-
So I bought one of these off ebay in the 6 pin version because I'm thinking of building another amp which can accept normal bias Stax phones and Justin is no longer making the 6 pin version. It was ordered on August 22 and arrived today. The socket as received was too tight to accept my Stax SR-5 jack. I pulled out my drill set and used the blunt end of the drill starting with #48 (0.078" = 2 mm) drill to gradually expand each pin, working up to #39 (0.099" = 2.5mm), after which the Stax jack fit snugly. I'm going to let it sit for a few days and see if the socket tightens up or if it stays snug. The front diameter measures 0.710" = 17.8mm, which also appears to be the distance between the 4 screw holes. The screw holes will take a #4 screw comfortably. Workmanship appears to be otherwise good, although not up to Headamp standards, but neither is the price. It's been awhile, so remind me of the reason. Is this one of those that has a fairly large capacitor on the bias supply that can discharge and fry the diaphragms?
-
Most of the design credit belongs to the engineers at Stax who designed the original circuit. I just did a logical update with technology that wasn't available when they did the original design.
-
Great to hear that another SRX Plus is alive. The DN2540s definitely vary in the resistance needed to achieve the proper current. How do you like the sound?
-
Well, that's an altogether different question. Both Birgir and Dr. Gilmore have documented the shortcomings of the eXstatA design - the solid state version measures worse than the Stax SRM-323, and the hybrid version takes 6S4A tubes, which are excellent output devices, and uses them in an intermediate stage, seemingly for no other reason than to say there are tubes in the design. Let me just add that the output "current source" is based on a circuit topology that Walt Jung, a well known solid state engineer, gave as an example of what NOT to use (AudioXpress issue 4, 2007), because it just isn't a very good current source.. On the other hand, Dr. Gilmore posted in the HEV70 query thread in the amplification section of Head-Case on Mrach 7, 2006, that, "I have 2 of them. Never had a problem with either. They sound like crap but that is a different issue." And in his original article on his all triode direct drive tube amp design he said of the HV60/HEV70, "The solid state drive amplifier is horrible. Headphones themselves are excellent." You might be better off selling the hybrid eXstatA and putting the funds towards a better amp, either a used Stax or one of Dr. Gilmore's designs. If you can buy or build a Stax to Sennheiser cable adapter you can use it to drive your Sennheiser stat phones as well (or, use the SRD-7 pro with a cable adapter for the same purpose).
-
It's really pretty simple. You need to identify which pin(s) in the socket is (are) the bias pin. For the Pro socket, it's just one pin, for the normal bias it's the same pin plus the center pin. If you have a voltmeter, just connect one lead to ground and probe the other pins one at a time. The amp output pins should all be close to zero whereas the bias pin will be a few hundred volts, so there shouldn't be any issue with identifying which is which. Note that the actual value of the voltage doesn't matter, it won't be accurate anyway, but there should be a clear difference between close to 0 volts and a few hundred volts. You can do this test with the box closed for safety. Note which pin is the bias pin. Then turn off the amp, unplug it,wait for the power supply to discharge, and open the box. You solder a 5.1 megohm/500 volt rated resistor between every pin and its connecting wire EXCEPT for the bias pin - that should be 4 resistors. Actually it won't hurt if you solder a 5.1 megohm resistor to the bias pin since it doesn't carry any current, but it isn't necessary. Just make sure they don't touch each other - if you want to put some heat shrink around them so the connections aren't exposed that's fine. That's it.
-
And the headphone box has a mirrored lid so you can admire yourself wearing the headphones.
-
Probably the easiest way is to add the 5.1 megohm resistors (needs to be rated for 500 volts) at the headphone socket, between the socket and the wires going to the socket from the amp board.
-
Cool! I bet this is a first - of course Stax built transformers to use with speaker amps but I haven't heard of a headphone amp used with transformers to drive speakers. I wonder how a T2 or BHSE with transformers would sound driving, say, original Quad ESLs, which don't need all that much power.
-
That's an interesting variation, will be interested in hearing how it turns out. I would make one comment - without any global feedback you could have some issues with channel-to-channel balance as Dr. Gilmore has mentioned in his articles about the KGSS and BH which were on Headwize (not sure if they are still there or not).
-
DefQon said: "What's the cap diameter size you use to cover the 6th pin on normal bias outputs after the pro conversion?" I use a #4 nylon screw, superglued in place
-
Ah. Pesky decimal point
-
Hmm. 2 x 360V @ 1 amp = 720 watt transformer, and that's without the 36 watts from the 18-0-18 winding.