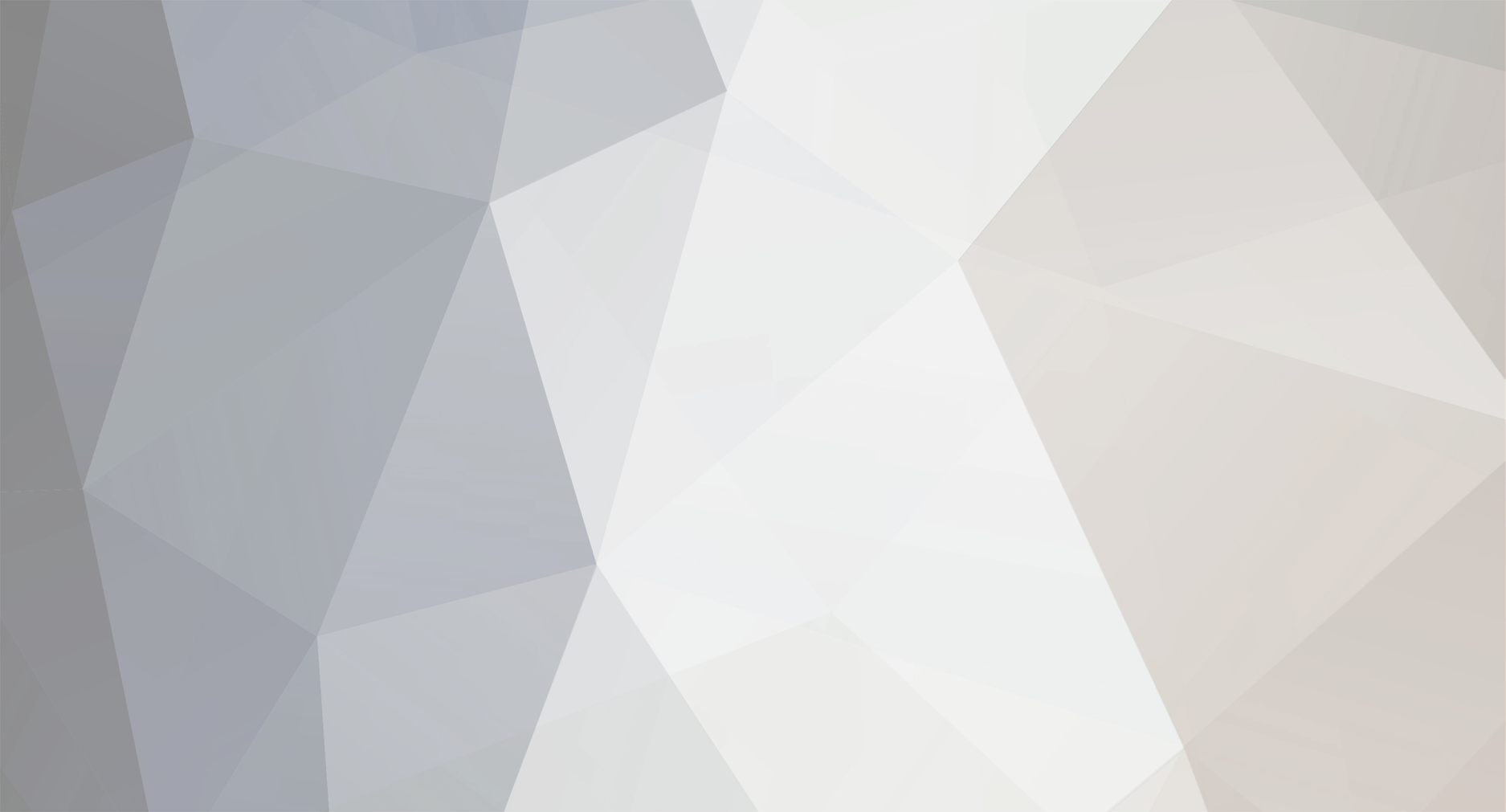
jamesmking
High Rollers-
Posts
387 -
Joined
-
Last visited
-
Days Won
1
jamesmking last won the day on July 27 2021
jamesmking had the most liked content!
Converted
-
Hobbies
breaking 2mm carbide end mills
-
Headphones
stax sr007a
-
Headphone Amps
DIY T2, DIY joamat mini t2, DIY single box blue hawaii se, megatron, DIY hi-amp alpha centauri
-
Sources
garrard 401, loricraft psu+plinth, hadcock 242 se, ortofon cadenza bronze, leema agena, mf v90 dac + golden reference LV psu + synchronous rectifier
-
Other Audio Gear
quad esl 2805, leema hydra, townshend allegri, dcs 905 adc, ps audio p3, van den hul first cables, cardas golden reference mains cables, cardas golden reference speaker cable
Recent Profile Visitors
The recent visitors block is disabled and is not being shown to other users.
jamesmking's Achievements

Limited Edition Bronze Participant (4/6)
550
Reputation
-
Here are a few suggestions. My apologies if you have tried any of these already. If the hum is changing after a few minutes then this implies to me that thermal expansion could be the cause. Are you sure all the pins of any socketed components are gripped well by their sockets? I believe there have been cases where over time some of the teflon tube sockets pins have started to lose their grip.. I would also very careful with the amp off and all capacitors in the psu drained and using a high resolution multimeter check the resistance between the psu connectors and the amp boards to make sure there is not a poor wiring connection due to oxidized wires etc this test will also check for any potential problems with an umbilical if you have the psu in a seperate box from the amp with seperate wires for the left and right channel. I think at this stage you need to start being very systematic and seeing what is going on.. so do you have access to an oscilloscope? I don't have a KGST but I assume it has separate and identical + and - amplification stages for each channel with a phase splitter at the input stage to allow single ended or balanced input... With a scope you can CAREFULLY (10x probe and dont connect the probe ground lead to anything that is live) probe the output pins at the stax socket one by one AVOIDING the bias pin and see if you have hum on both the + and the - outputs of a channel or if it is only the - or + half. This could potentially eliminate half the components of a channel from being faulty. If both - and + of a channel has hum then suspect something common to both which is usually the psu or input phase splitter. If you have seperate psus for each channel then you need to look at the psu rails to see if there is excessive ripple on one of the psus. If each channel shares the psu and only one channel has an issue then its very unlikely to be the psu but it could be the wiring from the psu to the effected channel. If all else fails a scope is an essential debugging tool and you are going to have to compare the good and bad channels and see what is different. good luck regards James
-
Thats whats needed but, stax logic is simple: why make a better product when you can sell something worse for much more and the hifi magazine reviewers are guaranteed to say its the best thing since non-sliced, small batch, organic artisan, seeded, whole meal, bread... *sigh* between on semi and Stax we just can't have nice things.
-
CNC metal machinists (for Stax amp cases) unite?
jamesmking replied to jamesmking's topic in Do It Yourself
true, which is why I have been upgrading the axis bearings etc. I agree prevention is better than detection, which is why I am going for steppers with double torque than the originals, plus the software that comes with the closed loop system provides graphs, including positional error which will allow me to fine tune the pid parameters and see what is actually going on and give me more options to fine tune and correct. I am also learning a lot - which is fun too. I loved metalwork and woodwork at school but when the route of computer science, but have always enjoyed making things - even if it's just putting together flat pack furniture for friends or soldering pcbs. -
CNC metal machinists (for Stax amp cases) unite?
jamesmking replied to jamesmking's topic in Do It Yourself
junk z axis. holy crap, I just disassembled the Z axis. The entire spindle weight is held by a 12mm ball screw. On each end of the ball screw is just one f688z bearing - (8mm ID, 17mm OD with a flange 18mm diameter). These tiny bearings have no preload and not designed for axial loads and have axial play. Looks like fox alien are relying on the weight of the spindle alone to push down on the lower bearing and that's the only thing stopping the spindle from dropping. Piece of absolute SHIT! The bearing housing has no recesses, no preload mechanism, no adjustment mechanism, nothing it's just unbelievable. Looks like I'm going to need an entire new Z axis too... Does anyone know if there is a angular contact version of the f688z?? sigh single tooth carbide partial profile (so it will do multiple thread pitches and the tool pressure is a lot less than other threading tools.). It's more versatile and cost effective than buying complete profile thread end mills. With 5 thread mills I have every metric pitch (both fine and course) covered from m3 all the way to m10. https://www.shop-apt.co.uk/single-tooth-thread-mills-dlc-for-aluminium-internal-60/internal-single-tooth-carbide-thread-mill-partial-profile-05-10mm-pitch-dlc-coated-for-aluminium-39mm-head-diameter.html The thread mills don't come with all the necessary parameters (e.g. tooth height, distance from the centre of the tooth to the bottom of the end mill etc.) for the software I use so I had to take multiple measurements with a 0.001mm micrometer and average the results and guestimate other parameters. The threads are m6 I ran 7000rpm, 150mm/min feed, 70mm/min plunge 0.0054mm per tooth chip load, bottom to top cutting a right handed thread. This resulted in the threads being cut in two passes and the chips falling into the bottom of the hole (which I made 1.5mm deeper than needed to hold the chips). To make the thread go all the way through the 10mm mounting plate I found I had to start about 1mm below the bottom of the material, so I painters tapped and superglued a 3mm sacrificial aluminium plate underneath. -
CNC metal machinists (for Stax amp cases) unite?
jamesmking replied to jamesmking's topic in Do It Yourself
Well, I decided I needed to upgrade my CNC machine (replace almost everything from the original machine I purchased). having already upgraded the controller, spoil board, spoil board mounting and spindle it's time to look at the axes .... First I got myself an 80mm diameter er20 ceramic bearing 2.2KW water cooled spindle with labyrinth seals to replace the cheap 65mm 1.5Kw er 11. To fit the 80mm spindle I had to make a new mounting plate. This included experimenting chamfering and threading. I settled on 0.3mm chamfers at 45 degrees and experimented with thread milling. The result I think is ok: (full discloser I purchased tooling plate so the top and bottom surfaces were already machined flat, but all the other surfaces got machined. I have ordered 4 nema 23 closed loop steppers (3NM - about twice the holding torque of the original open loop steppers the machine came with), which will entail replacing most of the wiring loom, removing the existing open loop motor drivers, removing the motors, some software config of the new closed loop drivers and some changes to the controller wiring. The original divers have no error output pin so the controller has no idea if a stepper has an issue. The new drivers include error output pins so they will need to be connected to the controller. (stock jpeg from the ebay listing, I'm still waiting for delivery) I have also replaced the standard 'deep' groove (6001 series) bearings inside the bk12 bearing housings with angular contact bearings (7001 series) as per this you tube video: I also noticed that all the bearing blocks were attached to the machine with m5 bolts despite the blocks being designed for m6, So I plan to replace those bolts and find a way to make new threads in the machine housings. The nema 23 motors are also designed for m5 bolts but the machine uses m4 (on avery axis except Z), again I don't know why fox alien decided to use one size smaller bolts on everything that drives the axes so I will have to machine new back end plates/motor mounts too. After these upgrades and fixes the only original parts of the machine left will be the frame, axe and the metal case the electronics came in. It's so nice to have a cnc machine so I can make parts to upgrade my cnc machine... -
portable if you are godzilla or king kong....
-
CNC metal machinists (for Stax amp cases) unite?
jamesmking replied to jamesmking's topic in Do It Yourself
I thought I might post some of the modifications I have been doing to my Flox Alien vasto. I got fed up with the not so rigid spoil board and so filled in the bottom with 20mmx40mm aluminium extrusion... and replaced the thin t slot and mdf spoilboard with a 30mm thick mdf slab. The result is far more rigit and will take my own weight (60kg) with ease and no detectible flexing. The plan for the spil board is to have m6 threaded inserts on the underside of the board to allow me to screw in work holding clamps/brackets. A 20mm by 20mm grid engraved and a set of 3.175mm holes around the edge so I can insert small pegs to make lining up work with X and Y axis easier. I also got fed up with the cheapo controller. It has no rs485 support so it could not control my spindle vfd. I could not change spindle speed or direction in software. In fact the original unmodified machine could only switch on and off the cheap dc motor it was supplied with and had a potentiometer for manual speed control with no indication or rpms. It has no wifi support and no user interface, is also only 3 axis and completely undocumented. I opted to rip out the controller and put in a rootcnc controller (https://www.rootcnc.com/root-controller-iso-about/) running fluidnc (http://wiki.fluidnc.com/) control software. It took a while to configure fluidnc and re do all the control box wiring. I replaced the 2 pin spindle power socket on the back with a 4 pin to carry rs485 from the controller to the spindle vfd. I also removed the pause and resume buttons and replaced them with sockets for a tool height probe and a 3d probe. While I was at it I replaced the now redundant potentiometer that used to control the voltage on the original 48V spindle output with a fixed voltage divider of 12V so I could run a good quality noctura cooling fan and power diode lasers directly. I also got a cheap minbot labeller and went on a labelling spree. The result is I can store multiple profiles (one for the laser and one for the vfd spindle) in the controller flash, In fact rootcnc and fluidnc is versatile enough and has enough I/O I could run a vfd and laser at the same time if I could find a sensible way to mount both. I can control the spindle speed and direction in software and by using standard S and G3,4 and 5 gcodes, control the machine via the built in web server, usb or wifi and have much less fan noise, power 80W diode lasers directly from the control box and have 2 more axis. The spindle control and a spare axis makes an automatic tool changer such as the rapid change atc https://rapidchangeatc.com/ a viable option. I now have enough expandability that I could add control for a rotary axis, run a pendant or even consider automated tool changes... I have been experimenting with automated tool height measurement and have written some gsender macros to set the tool length offset using the tool height setter I recently purchased. I still have to manually remove and insert and screw down the tools but the aim is that I will then just press a button and the machine will measure the new tool height and Z axis work coordinate so the tip of the tool is at the same physical Z height as the previous tool. I chose the tool height sensor because it is also compatible with the rapid change atc.. Gsender has poor documentation for its macros so I got the source code and reverse engineered the macro language parser. I love open source software, if you can't find the information online you can always find it in the source code. The Z axis mount is too narrow to accept a mounting bracket for an 80mm diameter spindle. So at the moment I am stuck with 65mm spindles which limits me to only er11 collets and a maximum end mill diameter of 6mm. So when I have finished rebuilding the machine I will make a new zaxis mounting plate for 80mm spindle brackets and am looking at buying a 2.2KW er20 spindle with ceramic bearings and better dust sealing. Further in the future I would like to get the rapid change atc which will probably necessitate extending the y or x axis extend the x axis from 420mm useable to around 550mm or so. I'm also thinking about changing to closed loop steppers. happy cnc'ing James -
That would be very nice, but, I suspect given the general behaviour of the human race, that there is a giant no fly zone around the sol solar system. I also think "humanity" probably has developed immunity to kindness/forgiveness. The story goes that the Argentinians could not get the Exocet working so as part of the support package they had several french advisors fly to argentina during the war to help them use them against the uk ships.... (https://theweek.com/world-news/falkland-islands/45704/bbc-finds-evidence-french-helped-argentines-sink-our-ships) remember it pays to pay for the support package
-
latest stax announcement: Due to decreasing sales of the sr009 we are discontinuing the sr007 since we don't know how to increment the price to make as much profit on it as the sr009 series. (We also forgot how to make spares and repair it cost effectively). We are proud to announce the release of the sr007a mk3. This release solves all the warmth issues of the previous sr007 models and benefits from the added clarity, detail and speed which made the sr009 series such good sellers. Please ignore the sr007 mk3's cosmetic similarities to sr009, we assure you the mk3 is a completely reimagined and redesigned sr007 brought into modern profit levels using modern technology for only $9000. Available now from all two remaining authorised dealers in Japan. Stax would also like to announce a new energizer to partner with the all new sr007 mk3; the srm007C rap using state of the art TPA3255 driving a 1:10 step-up transformer. The srm007C rap is manufactured under license by our new partners the IAG group in their mega factory in Shenzhen. It offers class leading efficiency for those who can't afford the utility bills associated with a valve design. Finally and terminally Stax would like to announce a collaboration with Blackstone private equity where Stax will rent back its manufacturing space from Blackstone in return for access to Blackstone expertise in increasing profitability and reducing manufacturing costs..
-
So Stax kill about the only good headphones they sell. Welcome to second-hand sr007 prices skyrocketing...
-
Well its not DC coupled (i.e. NO capacitors in the signal path) and it has a very low voltage swing - 200Vrms... due to the fact it has pre-amp tubes in its output rather than power tubes like the EL34. The bandwidth is not great and there is no distortion specifications at all (nothing vs output voltage and nothing vs frequency) which is a bit suspicious. I suspect the amp will have trouble driving Stax sr007. There is little information about the power supply but it does not appear to be fully regulated. As such it certainly does not look to be even close to a blue hawaii, mini T2 or T2 in specs and capability. Even the all valve Megatron has more voltage drive and almost certainly a better power supply. It is not known if the amp uses anode load resistors (bad) or constant current sources (good) for the output valves, but I suspect it's resistors. On the plus side it does not appear to have an output transformer... unlike some crappy comercial designs and does not require any DIY skills. However, if you don't mind building your own amp you can almost certainly make something substantially better (fully regulated power supply, fully DC coupled, constant current sources for the power valves etc) for around the same price.
-
perhaps your last post is exactly why no one else replied. I would like to see a long term solution to the entire Palestine problem. For your information I have never protested on the topic in question for either faction and have no desire to, its complicated mess and saying one side is exclusively right is impossible and unhelpful to a long term solution. I could call you a bigot for implying the UN and therefore, probably by extension, the entire world plus all universities is anti-Semitic but that would achieve nothing, but your words, do show your silo mentality which I am afraid to say is all I have experienced every time this topic has been discussed, my father has experienced similar as well and I am slowly coming to the conclusion this kind of experience might be widespread. I could be insulted by your words saying you expect me to protest in support of the palestinians or to remove my head from my arse, (If I could bend around that flexibly the climbing problem I got stuck on today would be a breeze). But I refuse to be insulted. I would say insults are the arguments employed by those who are in the wrong, but I dont think all you say is wrong. I am afraid to say that, in my opinion it is people exactly like you who make it so hard to feel any connection or sympathy for the Jews, but I try to keep an open mind, since, just because the proponents of an argument speak objectionably, it does not mean their argument is without merit. However, I have no desire to further engage with you on this topic or any other.
-
I'm sorry, but I am not sure what you are trying to imply. Just because no one comments does not mean that no one has an opinion (informed or otherwise) or that silence means that you are right or that everyone agrees with you or that there are not counter arguments to what you have written. The lack of comments could simply be that no one wants an argument with you (especially with your privileged role as a moderator), or start a flame war. If the protagonists on both sides in Palestine where equally reserved perhaps there would be fragile peace or even better a pathway to some solutions to the problems. Each side can point to the past, to past atrocities from the other side, atrocities that fuel more retribution and atrocities and naturally lead to attack is the best form of defense arguments. Until there is forgiveness and a willingness to not look at the past the deaths on both sides will probably continue at infinitum. International law says Israel illegally occupied the west bank (United Nations resolutions, including 446, 452, 465, 471 and 476 and United Nations Security Council Resolution 2334 of 2016 reaffirmed this yet again) and then illegally (advisory opinion by the primary judicial organ of the UN in 2004) built settlers homes on what amounted to the front line. If this had occurred elsewhere in a different context the international community would be sending an army to throw the occupiers out... Given this it is hardly surprising Hamas and the Palestinians also use the argument that the Israel is responsible for the deaths and that attack is the best form of defense. And so the atrocities and deaths continue on both sides, each blaming the other and each attacking the other and calling it defense and the human suffering continues.
-
goldenreference low voltage power supply
jamesmking replied to kevin gilmore's topic in Do It Yourself
I just have a Mastech MS5308 Lcr-Meter. kemet 35v 47uf tantalum esr 100hz 0.4ohm 120hz 0.4ohm 1khz 0.22ohm 10khz 0.19ohm 100khz 0.12ohm panasonic 47uf 63V electrolytic esr 100hz 1.1ohm 120hz 1.0ohm 1khz 0.39ohm 10khz 0.33ohm 100khz 0.30ohm chinesium "suntan" brand electrolytic 47uf 105C 25V esr 100hz 4.8ohm 120hz 4.4ohm 1khz 1.75ohm 10khz 1.41ohm 100khz 1.26ohm so for this tiny sample size (and not the same voltage rating) tants have lower esr throughout the range I can measure. so not enough data points, resolution, sample size or frequency range etc. to make any real conclusions but maybe enough to start a electro vs tant thread... -
goldenreference low voltage power supply
jamesmking replied to kevin gilmore's topic in Do It Yourself
I think tants typically will have lower effective series resistance at high frequencies than electros, and in general tants esr decreases with increasing frequency unlike electrolytics. https://www.doeeet.com/content/eee-components/passives/why-low-esr-matters-in-capacitor-design/