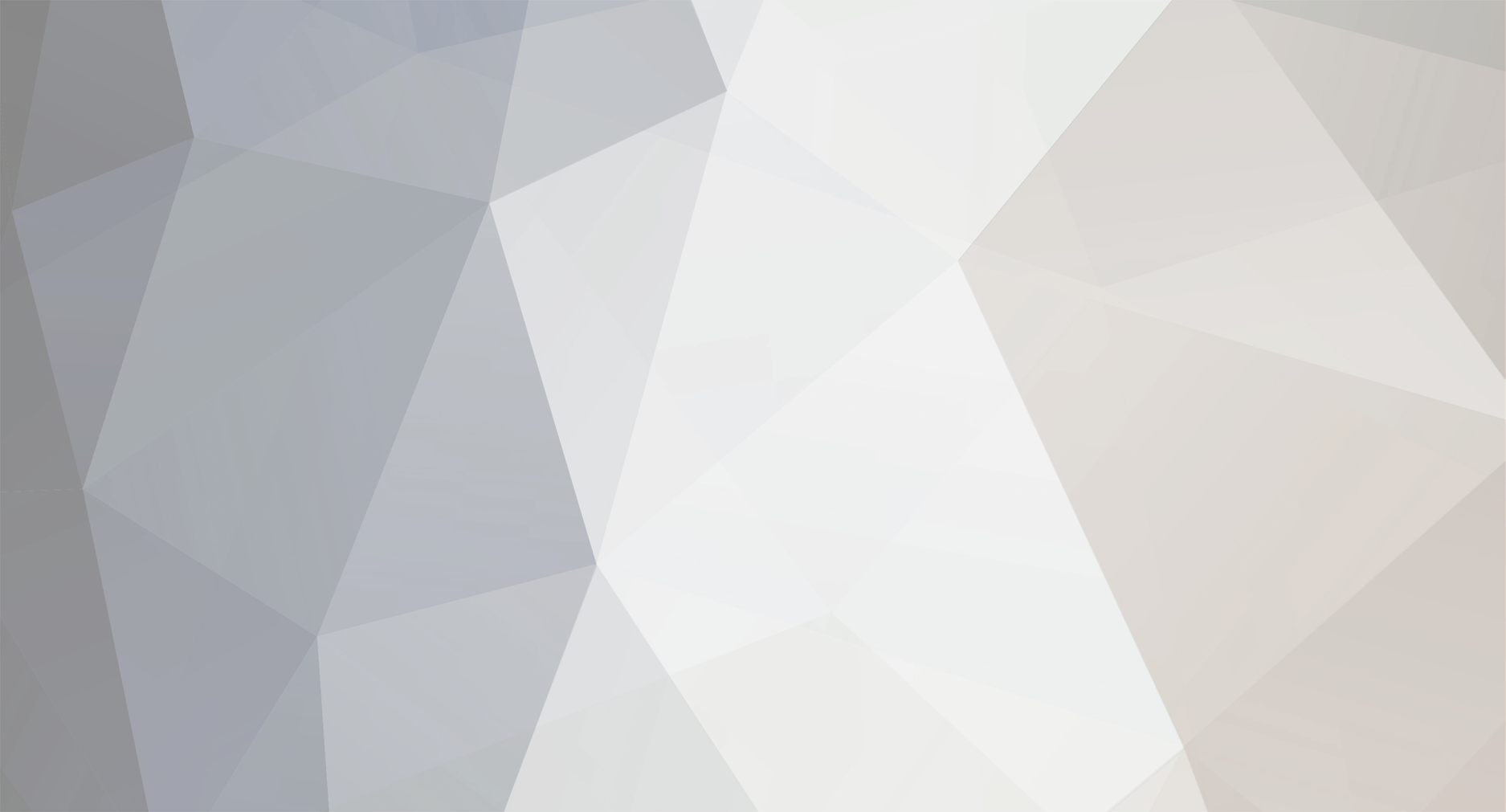
jamesmking
High Rollers-
Posts
408 -
Joined
-
Last visited
-
Days Won
1
jamesmking last won the day on July 27 2021
jamesmking had the most liked content!
Converted
-
Hobbies
breaking 2mm carbide end mills
-
Headphones
stax sr007a
-
Headphone Amps
DIY T2, DIY joamat mini t2, DIY single box blue hawaii se, megatron, DIY hi-amp alpha centauri
-
Sources
garrard 401, loricraft psu+plinth, hadcock 242 se, ortofon cadenza bronze, leema agena, mf v90 dac + golden reference LV psu + synchronous rectifier
-
Other Audio Gear
quad esl 2805, leema hydra, townshend allegri, dcs 905 adc, ps audio p3, van den hul first cables, cardas golden reference mains cables, cardas golden reference speaker cable
Recent Profile Visitors
The recent visitors block is disabled and is not being shown to other users.
jamesmking's Achievements

Limited Edition Bronze Participant (4/6)
593
Reputation
-
You could measure the gain. input say a 1KHz sine wave at 250mV, Measure the output it should be about 250V with the volume all the way up...
-
As far as I know most of Kevin's valve and value/transistor hybrids aim for a gain of 1000x - thats what the mostly modern T2 has and I think the blue BJT blue Hawaii. The only exception I have experienced is the (standard) EL34 Megatron which has lower gain.
-
goldenreference high voltage power supply (GRHV)
jamesmking replied to Pars's topic in Do It Yourself
for my megatron build (which uses a 300V golden reference hv psu rail) I used 250VAC which gives peaks of about 350V with nominal AC mains voltage. -
be careful, the ssth512 has an insulated body and no live tab. The DSEP12-12 has a live metal tab and will have very high voltages on it.
-
the problems with the stax srm006t is that like the srm007 it has too many design compromises that massively effect the sound. 1. its high voltages are not well regulated 2. it uses resistors as a anode load for the valves which reduces current drive and efficiency rather than using a constant current source. (the srm007t is exactly the same design but parallels up the values to get a bit more drive but its still not fixing the problem and costs twice as much) 3. it uses values which don't have much current drive or are that high voltage. Most of the good designs use far more powerful values such as EL34 running at conservative currents (for what they can do) rather than running tubes design for pre amps really hard. The result of this poor bass, poor dynamics, mushy and in general, a sound that, as you turn the volume up the bass gets more soggy but not that much louder. The drive situation gets far worse if you use a difficult to drive headphone like the sr007 (I tried this and you cant get even close to the performance the 007s can provide with a well designed energizer. Replacing a silicon diode bridge with Schottky diodes might give you a bit less switching noise and slightly lower voltage loss but its not addressing the major design issues. If you really want to upgrade the energizer get the anode resistors replaced with a constant current source. This massively increases the drive and addresses some of the poor design of the energizer. If you are in to diy electronics and want to build your own energizer there are a variety of energizers so much better than the srm006 or srm007. one of the simple and fairly cheap options, with better valves and fully regulated high voltage power supplies is the alpha centauri from http://www.high-amp.de. Its relatively simple to build and walks over and kicks in the head the srm006t. I am speaking from experience here. I started with a 006 and built the centauri. The published design still uses resistors for the anode load but the website does offer pre built constant current sources for it. Unfortunately the schematics and the pcb files are not available for the constant current sources. Next come the energizers with constant current anode sources, fully regulated high voltages and beefy output valves: The blue hawai, it will cost more to build than the alpha centauri, is bigger and more complex but sounds even better At the apex of stax energizers is the diy T2. The original one uses transistors which are no longer available and so getting non fake transistors for it is not easy or cheap. The design has been updated to use more modern transistors. I built the mostly modern version which has a mix of old and current production transistors. It big, complex and fairly expensive to build but the performance is fantastic. I replaced by blue hawaii with it and never went back. There is also a mini T2 which is a simplified version using modern transistors and smd (surface mount components). Its not as good as the full T2 but I think its better than the blue hawaii. if you want something that is fairly simple and will warm up a room on cold nights then there is the megatron. I never got around to finishing my build but its one of the more simple designs. There are many more diy designs out there and in this forum. But the bottom line is if you want a realy good energizer for your Stax headphones, Stax does not sell one and most of the other commercial designs are almost equally as bad (and in some cases worse). P.S. the offset or balance DC voltages being a few volts out or drifting around by a few volts is not going to effect the sound or reliability. Remember the headphones are designed to take 100s of volts, 5V or 10V of DC offset or DC balance is nothing to them.
-
Megatron Electrostatic Headphone Amplifier
jamesmking replied to kevin gilmore's topic in Do It Yourself
22ohm to ground on the heater/filament looks like its there to stop the heater floating and might reduce hum and is therefore probably optional. It looks like this resistor is not present in the megatronpowersupply300v2xl gerbers. It also looks like there is a 221 ohm resistor between the anode and G2 of the el84 in the gerbers which is not present in the megatronps300.pdf. I am afraid I did not build this power supply so I can't comment on which is the more up to date or preferred version. But in general its the Gerbers which people get pcbs made from and therefore is assumed to be correctly functioning unless the threads on headcase say otherwise. -
you might want to try stereo: Gunter Wand;Ndr Symphony Orchestra (specialist in Germanic symphonies c.f brahms, bruckner) herbert blomstedt;Gewandhausorchester Leipzig Staatskapelle Dresden;herbert blomstedt André Cluytens;Berliner Philharmoniker igor Markevitch;Orchestre des Concerts Lamoureux mono: erich kleiber;vienna po (dad of carlos kleiber) felix Weingartner;london so (first complete recorded beethoven symphony cycle) paul van kempen;berlin po (conductor of kempff classic 1950s beethoven piano concerto cycle) The marmite option: if you like "period instruments historically informed": roger norrington;london classical players
-
Electrolytic caps are well known for being relatively fragile. Almost any reverse polarity voltage will damage them over time. They also degrade with temperature and time too. The input caps take the highest hammering because of the higher input AC voltage peaks compared to the output caps - (which only have to handle well regulated DC). Check if the diodes in the bridge rectifier are leaking, if one of the diodes starts to leak more than a couple of volts that would degrade your input cap. Also, when you have got the amp up and running again it might be worth monitoring the temperatures close to the caps, a rough rule of thumb is every 10C degrees rise in temperature halves the cap life. I have had good reliability experiences with kemet al10 series caps - although they can be expensive they are rated at around 15000 hours at 85C - significantly higher life expectancy than your caps and life expectancy. Part number ALC10A681EL550 is 550V 680uF. The ripple current of the kemet is 50% higher than your caps, but the esr of the kemets is higher, leakage current is the same. Unfortunately kemets tend to go in and out of stock again and the pricing can also be somewhat erratic. note the ALc10 kemets tend to be tall rather than wide - the ALC10A681EL550 is 80mm tall and so you would have trouble fitting it into a 2U high case.
-
farnell in the uk has plenty of stock of the FJPF2145 https://uk.farnell.com/onsemi/fjpf2145tu/trans-npn-800v-5a-125deg-c-40w/dp/3368628
-
FJPF5027OTU seems to be a possibility, seems to have similar specs except lower current rating and the same pinout. Hfe of FJPF2145 is 20 - 40 which is the same as the O variant of the 5027
-
CNC metal machinists (for Stax amp cases) unite?
jamesmking replied to jamesmking's topic in Do It Yourself
-
CNC metal machinists (for Stax amp cases) unite?
jamesmking replied to jamesmking's topic in Do It Yourself
Diamond drag engraving is surprisingly fun and easy. I decided to buy a spring loaded diamond drag engraver and do some experimentation on feeds, cutting depth, stepover etc. I ended up. 90 degree drag bit. tip flat estimated at 0.128mm, 0.1mm step over, fill crosshatch at 0 degree, 700mm/min feed speed. Far better results than using a V bit, much less sensitive to the material not being totally flat and far far faster. -
Well spotted! I didn't notice they are not using the 10Hz standard. I wonder why are they using 100Hz?
-
well specifically, The Denon cart user manual talks about the included headshell will provide the appropriate overhang - well thats BS because there is no standard. They may be referring to SME arms with bayonet fitting. The vinyl engine has specs for the technics arm geometry and its NOT the same as the sme bayonet geometry on say a SME 3009. The effective length, offset angle and overhang are all different, and in fact the sl1700 mk2 has a different offset angle from the mk 1 and therefore different zero tracking error points on the record. The cartridge could be used with the existing technics headshell. The user manual only specifies the weight of the cart and headshell which is not helpful in working out the resonance frequency if the technics headshell is used. The frequency response spec in the user manual does not include + or - dBs and so is meaningless and there are no specs on tracking ability either. There is some information about the diamond BUT nothing on the effective moving mass. the spec sheet contains even fewer specs than the user manual (omitting any information about the diamond)... Finally buried in the Denon blurb in spec sheet is says the headshell is 6g so the cart is 12.5g the suspension is 5*10*-3m/N which is very stiff, but then the cart is quite heavy. The technics service manual says the arm is effective mass 22g so with the technics shell you are looking at a resonance of about 10Hz ish which is ok. According to the technics manual, the arm can ballance carts up to 11g with the technics headshell and the denon is 12.5 so you will need to use a lighter headshell or add extra weight to the back of the arm.
-
oops In my day job I usually lecture to 18+ audience and if no one gives me a limitation on detail I tend to go for high levels of detail because in reality its almost never as simple as X is better than Y, it's almost always the case X and Y offer different compromises and its (in my opinion) important to understand what is going on and understand the compromises.