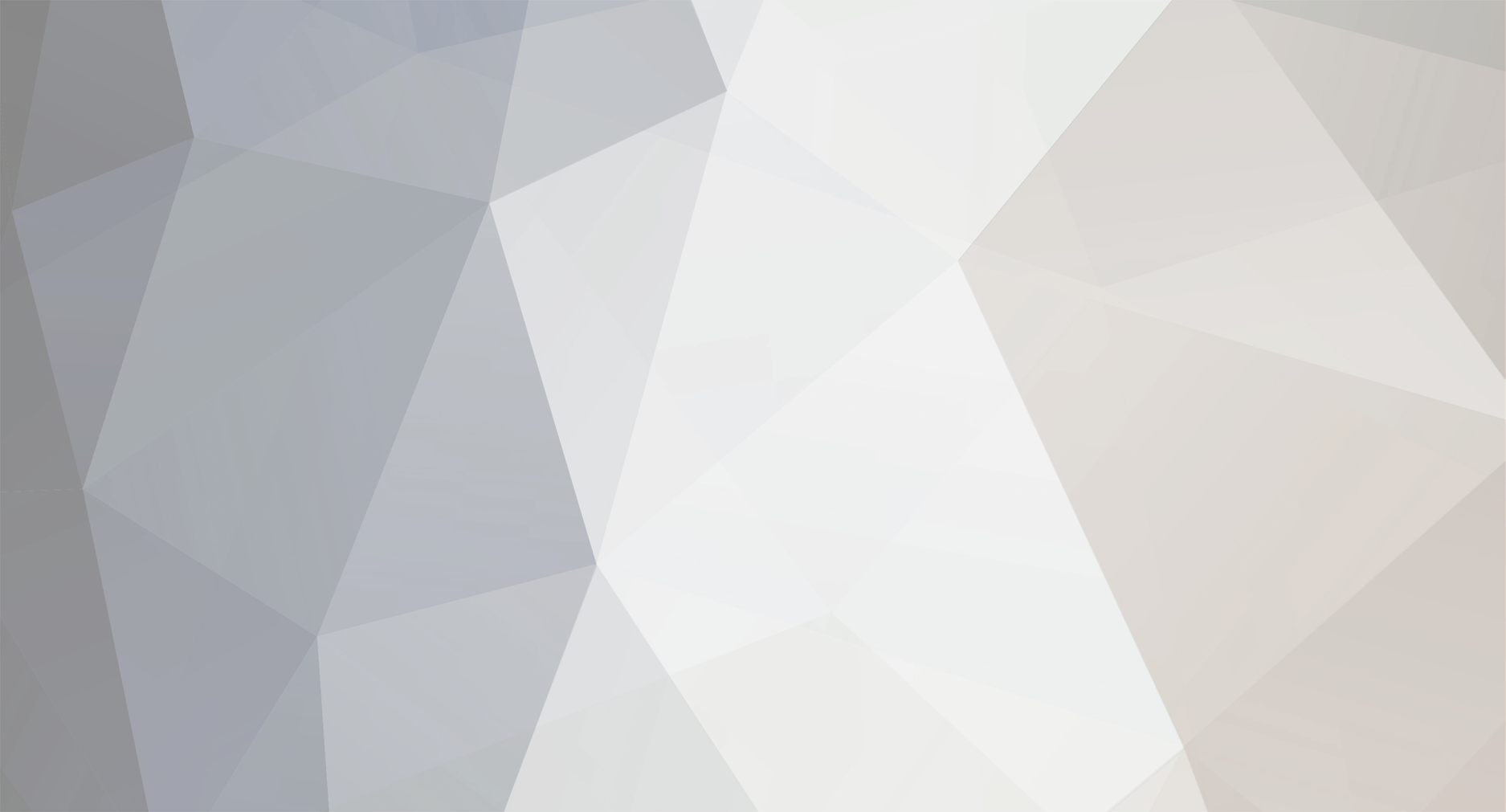
simmconn
Returning Member-
Posts
154 -
Joined
-
Last visited
-
Days Won
2
Content Type
Profiles
Forums
Events
Everything posted by simmconn
-
Congratulations! I can’t say that I fully agree with your analysis, but I guess getting the amp working is what matters.
-
LED: The numbers are all over the place: Your IV curve shows the LTL4213 should have Vf between 1.725V and 1.750V with 0.5mA of current. You've got three different voltage ranges for the LED. Which one is correct? You need to find out where the dependencies come from. Your previous LED chain voltage measurement shows 12.1-10.7=1.4V of voltage variations with not much If change. Is the 1.4V evenly distributed across 7 LEDs? If you suspect Vf change due to the temperature coefficient, that's easy to verify. Just keep monitoring the LED voltage with the amp powered on from cold. 2SK246: Your test indicates that the 'backup ones from ebay' are probably good. Unless the ones on the board are from the same seller and same batch, the test result probably doesn't help much more than that. Rather than replacing parts shotgun style. I'd take voltage measurements shotgun style, then sit down and analyze the data. Replacing parts without knowing why and what would be a very inefficient way of troubleshooting. For example, when looking into the active battery, measure voltage on all nodes. Beware of the burden by the DMM input impedance (usually 10M Ohms but YMMV), so plan carefully when you measure across high-value resistors. When looking into the final stage, collect enough voltage data within the CCS so you can calculate the current supplied by the CCS. Measure the voltage at Output+/Output-, then determine if the tubes are in the right operating point. If you know very well how the circuit works, you can strategically take only a few measurement at key spots; otherwise just do more leg work and collect all data. Don't worry if some could be redundant. They often end up helping you where least expected.
-
Yes the 2SK246 looks suspicious. Its |Yfs| should be around 1mS around Id=300uA, so changes in Vgs of 1.51V-1.43V=80mV should generate 80uA of change in Id. Apparently that's not the case here. You could use a 2SK373 or even a 2SK117 as a substitute. The 2SK208 is also a close sub, albeit in SOT-23 package. Also, Q16 Ib should not be that high. The current thru R39 is about 100uA, split between Q16 and Q17. If Q16 has an hFE >100, it's Ib should not be over 1uA even in the extreme case.
-
It looks like most of the voltage adjustment comes from the wandering reference, no wonder you said RV1 doesn't have much effect. Assuming your Q16 path works okay, comparing the two diagrams, V(R42) dropped (6.22-6.56)/6.56=-5.18%, almost the same as the LED string voltage drop (11.4-12)/12=-5%, which means the 2SK246 ccs didn't have much effect at all. To give you a data point, my mocked-up 2SK246 ccs changes V(22k) from 6.5496V to 6.5446V (less than -0.1%) when the supply changes from 12V to 11.4V. Your LED string seems not great, either. When the current drops from 703uA to 663uA (-5.7%, ignoring the Q16 base current), the LED string voltage drops -5% as well. Not much of regulation, isn't it? I grabbed a random red LED from my stash and in similar situations its forward voltage changes from 1.7914V to 1.7881V, only -0.18%. Your LED probably has 700uA right around the knee on its IV curve. It may not be a bad part, just not suitable for this location. The above assumes the Q16 and the rest of the battery circuit works okay. Oh well, let's fix one problem at a time.
-
The difficulty setting the V(R42) to 6.55V could be due to something else. I assume that you observed different pin out when substituting 2SA1486 with 2SA1413. As long as the LED strings are lit stably and not flickering, the RV2 should adjust smoothly for 6.55V across R42. The idea is to set the 2SK246 ccs to about 297uA with the majority of that going through R42 and only a tiny bit from the base of Q16. If you have some spare 2SK246 from the same batch, resistors and pot, breadboard a circuit and test with a bench DC power supply. See if the pot hits the bottom or something wrong with your 2SK246. It’s a good idea to measure around the active battery circuit, using the top node as the reference point, mark voltages and currents on the schematic. The active battery does not take rocket science to troubleshoot. You just need to know 1) Ohm’s law, 2) Transistors have hfe, and 3) A forward-biased silicon junction has a voltage drop about 0.6V. There is no need to be paranoid about the battery not being spot-on at 740V. Since it is transparent to the audio signal, they can even be purposely set slightly differently from each other to compensate unbalances elsewhere in the circuit. But if your amp don’t like them being near 740V at all, that means some other parts of the amp is quite different from what the designer has envisioned. There are quite a few feedback loops in the works that maintain a near-zero offset. Let go of the active battery voltage temporarily in exchange for zero offset can set those loops at their normal operating point and help you find out who’s not behaving correctly. Mark any voltage reading with a ‘*’ if you hear oscillation when you get the reading, as it may not be reliable.
-
Watch the power rail voltages as you see strange things happen, such as a low battery bottom voltage (-549V) coincide with negative output offset. Depending on your 10M90s in the PSU, you may need to reduce the current setting resistor values if they get into current limiting condition. It’s a good practice to load-test every power rails at 20% more than the rated current. Spend some time doing measurements across the board, mark the voltages at the key nodes in the schematic and verify the voltage and current that are marked in the pdf. Those are very valuable info.
-
No grid resistor R53 for the 300B? I wonder why the original design uses such a high value 22k. It’s going to interact with the Cga and cause some interesting negative feedback at high frequencies. Also, with the 300B, the max output amplitude could be quite limited. You’ll need about -100V bias to get the 300B to 400V @ 10mA on the plate. But the max negative grid swing is limited to about -160V due to the 2Sk216 Vds max. The result is limited positive output swing, or operating the 2Sk216 at risk.
-
Newly developed ground loop hum in a Stax SR-007A's right channel
simmconn replied to plaurids's topic in Headphones
Going two digits after the decimal point probably not going to be very accurate (check the datasheet of your meter for AC accuracy specified in % of reading + % of range and/or number of digits). I normally use a simpler way when calculating the SPL. Sr-007 has a sensitivity of 100dBSPL/100V, so 50mV of pure tone gives you 100-20log(100/0.05)=34dBSPL. The 007 has a f0 around 45Hz (a bit more gain compared to 1KHz) but audibility is also affected by the equal loudness curves, so YMMV. Without an FFT it’s hard to tell the harmonic composition of the noise, which affects its audibility. I guess you are not inclined to feed this into your sound card… -
Newly developed ground loop hum in a Stax SR-007A's right channel
simmconn replied to plaurids's topic in Headphones
I’d measure the output AC voltage across +/-, provide that your meter is up to snuff (has a 200mV AC range for instance). If there is indeed audible hum from the amp, you would get a reading least in double digit mV. -
It depends. Usually you want the attenuation to be at a later stage of the signal chain when possible, since the noise of the previous stage (DAC) will be amplified by the gain of the later stage (headphone amp). You can argue that the DAC's intrinsic noise is low enough that even if amplified by the full gain of the later stage (headphone amp), it is still well below the intrinsic noise of the later stage, in which case it doesn't make much of difference implementing the attenuation at either places. There are also practical concerns. Using a passive attenuator such as a volume pot increases the source impedance of the later stage, which often increases its noise and in some cases, affects its frequency response and linearity (more distortion). Many DACs with brilliant SINAD numbers employ distortion compensation. They are tuned for the lowest measured distortion at 0dBFS input. As soon as you reduce the (digital) input level, the harmonic profile changes quite significantly. The result of the above is that the system may 'sound' different with digital volume control vs analog volume control. Last but not least, one's ears are the most valuable device in the signal chain. Personally I'd rather have an old-school volume pot as close to the headphone amp/power amp as possible as the 'emergency shutoff valve'.
-
May I ask the reason for reducing R39? Is it because of the STN9360 HFE drop under very low collector current? I did find that STN9360 and 2SA1486 response differently to the compensations I added to improve stability, but that’s probably more due to their different Cob. Thanks!
-
That sounds normal. Probing the R42 (-) injects noise to the diff amp. Connecting R42 (+) to the same meter reduces the injected noise. Also the active batteries will not be *exactly* the same in term of stability even if you match the parts. To what level did the voltage of the two batteries of the R channel decrease? What are the voltages at the (+) and (-) of the two batteries when that happens? Remember I suggested you to check 1) the K246 CCS 2) whether the active battery still maintains the gain when the output decreases [V(+)-V(-)]/V(R42). If you only have one multimeter, how did you notice the voltage of the battery change when you probe R42? Both the input and output stage offset servo and the global NFB affects the DC offset. So it's important to see what causes the offset to be off beyond their correction capabilities. To be safe, also check the input impedance of your meter. The STN9360 generally have higher HFE than the 2SA1486. Everything else being equal, the stability will be a little worse. Using Q23 with lower HFE may help with stability, but I feel that the oscillation and the thermal-related stability may be two separate issues here. I don't quite understand that some people would spend thousand of $ on parts, building a unit that has a fair market value of close to 10k, while not willing to invest a few hundred $ on quality tools and equipment. If we know Stax only uses a multimeter to build and test T2, we'll probably avoid their amps like plague. How did that become ok when some lucky individuals do the same?
-
Please try to describe the procedure with more details. 1. Did you use a bench multimeter, or a portable one? The bench meter has slightly different characteristics between pos and neg leads, the portable one barely has any. 2. Did you put the pos lead on the pos node of R42 or the other way around? Did you connect the pos lead first or neg lead first? 3. when you mention “R42+ and R42-“, did you mean the R42s in the two active batteries of the same channel? Chances are the reference chain on the active battery is marginal, such that the input impedance of your meter would throw it off. Check your meter, also check the K246 CCS. The voltage across the LED string and the voltage across RV2 shouldn’t change. If the active battery oscillates, the DC voltage across R42s in the +/- arms of the same channel could be different. Do you have more than one meter? You can monitor the output of the active battery (across the test points) when you measure the voltage on R42.
-
Use your most sensitive organs. Do not connect the headphones. The sound emanating from the tubes when T2 oscillates a good hearing test, in terms of both sensitivity and frequency response 😆. Seriously, you could use the AC function of your multimeter. Most of them are good to tens of kHz, some good to a few hundred kHz. If something’s going on, there would be a good chance to see it on the AC meter once the reading settles. The active battery circuit can be marginally stable. The capacitance of the test lead can tip the balance and cause it to oscillate. But R42 should usually be safe to probe on. If you see a lower voltage, you might want to check if the output voltage of the active battery (+/-) has dropped proportionally, i.e it still maintains its gain. From there you’ll know whether the reference chain or the amplifier part of the active battery should be checked next.
-
Yep. Oppo is primarily considered as a cellphone company. The other CE products are their “side business”, at least from shipping volume point of view.
-
Building an energizer almost from scratch - advice on clamping zeners
simmconn replied to bobkatz's topic in Do It Yourself
I wish you doubled success with those. Oops, squared!😆 -
Building an energizer almost from scratch - advice on clamping zeners
simmconn replied to bobkatz's topic in Do It Yourself
Here is the impedance plot (phase and magnitude) of the transformer in an SRD-7SB with the SB circuit disconnected. Three sweeps were run with 1V input, output open; 1V and 2V input, driving a Stax SR-404 with its bias supplied externally. Take an educated guess, which curve is from which test condition? -
Output Stage Current Requirements for Electrostatic Headphone Amps
simmconn replied to JimL's topic in Do It Yourself
I see a few problems in your calculations. First, the load impedance is the characteristic of the phones, which is listed in your headphone’s spec sheet. It is not determined by the output voltage or current capabilities of an amp, which on the other hand are the amp’s design choices. Second, the reflected impedance to the amp is affected by many factors (and follows square of the turns ratio in an ideal case). In this case, the parasitics can have a significant effect on the load impedance the amp sees. Take a measurement and you may be surprised. Third, impedance is a vector. Using a scalar value is convenient but let’s not forget its vector nature and mostly reactive for the estat phones. The 1W of driving power would then be apparent power and not real power. Last but not least, may I suggest that we limit questions and comments regarding one project to a single or a couple of threads only? -
Building an energizer almost from scratch - advice on clamping zeners
simmconn replied to bobkatz's topic in Do It Yourself
That's all good statements in theory. My suggestion would be to plug-in the real-world numbers, do the math and find out what kind of voltage you really need/can afford, and go from there. For the protecting scheme, too. You now have a high voltage DC supply which can conveniently verify the protecting threshold of the candidate device. You could also connect the protection device/series resistor(s) to your phones and listen to them at comfortable levels. If you can't hear a difference, or even prefer the sound with the protection device present, viola! you've got a solution. FWIW, I found an MOV which looks like a 2W+ metal film resistor in my old Stax Lamba (normal bias). I guess at the time the non-linearity it brings was the lesser evil compared to a burnt driver. -
Building an energizer almost from scratch - advice on clamping zeners
simmconn replied to bobkatz's topic in Do It Yourself
An ideal shunt-type protection device for the estate phones should have: 1) Low (<10pf) and constant capacitance vs voltage and vs frequency - that pretty much crossed out all the silicon junction devices. 2) An I/V curve with a sharp corner, near-zero leakage within the operating voltage and well-controlled clamping voltage - that rules out most MOV devices 3) Fast acting. That excludes the gas-discharge type. What do we have left? Why use a shunt-type protector, just to give the amp and the transformer a jolt like a dead short when they are outputting close to their max voltage? The Stax transformer box adds a PTC in series with the transformer primary to mitigate this issue - and you know how people hated it. IMHO a better protection is to limit the output voltage of the amp. If the power rail voltage is limited, the amp's output is limited and the transformer's output is limited as well. -
Building an energizer almost from scratch - advice on clamping zeners
simmconn replied to bobkatz's topic in Do It Yourself
@bobkatzIMHO you are not likely going to get better performance with the TPA3116d2 class-D amp. It will have high noise and distortion than the amp modules in EHA5, plus the ultrasonic switching noise that may cause further intermodulation junk down the chain. Most if not all the imperfections you see in the measurement are caused by the transformer, such as higher THD at lower frequencies, the resonance at ultrasonic frequency that manifest itself as poor square wave response, plus other issues like phase shift (group delay distortion) that is not reflected in your tests. The transformer is the weakest link here, within the capability of the amp modules. Using a better transformer such as lundahl would help. I'm not sure if you can find one with turns ratio as high as 50. If not, you might want to switch to an amp with higher output voltage, if you need to maintain the 700Vrms output level. -
That's a common misconception about differential signals from signal integrity point of view. No output driver works out of vacuum. They are all power and ground referenced. Even with transformer isolation, there is imbalance in the windings and capacitive coupling between the primary and secondary, from windings to the core. In a practical world nothing is ideal. The AES diagram clearly shows how the current 'I' could create a noise voltage drop between the input shield point and the star ground point, which adds to the input signal in a common mode fashion. That's why there is a note in the end that says, 'as close as possible to each other'. How about at one single spot, can you get closer than that? Personally I wouldn't want to inject any dirty stuff from the ground of the source to IN- of my amp. So if I find out an RCA female to XLR male adapter connecting pin 3 to RCA signal ground while keeping pin 1 floating, I'd want to modify it.
-
Hmm, I wonder what kind of noise and hum level would be when you connect like that. Unless your source is true balanced pro gear with transformer-isolated output, most DACs and preamps have ground-referenced output stage. In other word, the +/- are not using each other as the return path, but pin 1 in that XLR cable. Once you include the PE connection and the signal ground connection in your common-mode return path, noise and hum inevitably gets included in the signal coming to the amp. Remember any amp has a finite common-mode rejection. However the theory says, I guess at the end of the day, whatever works best in my/your system matters the most.
-
I’m just saying, connecting like you described may not have the best hum rejection, and if we need to connect the PE and signal ground again at the amp chassis XLR input for better hum rejection, it defeats the purpose of running two grounds separately. That’s why I was asking if you have any measurement data to support your ground wiring scheme.