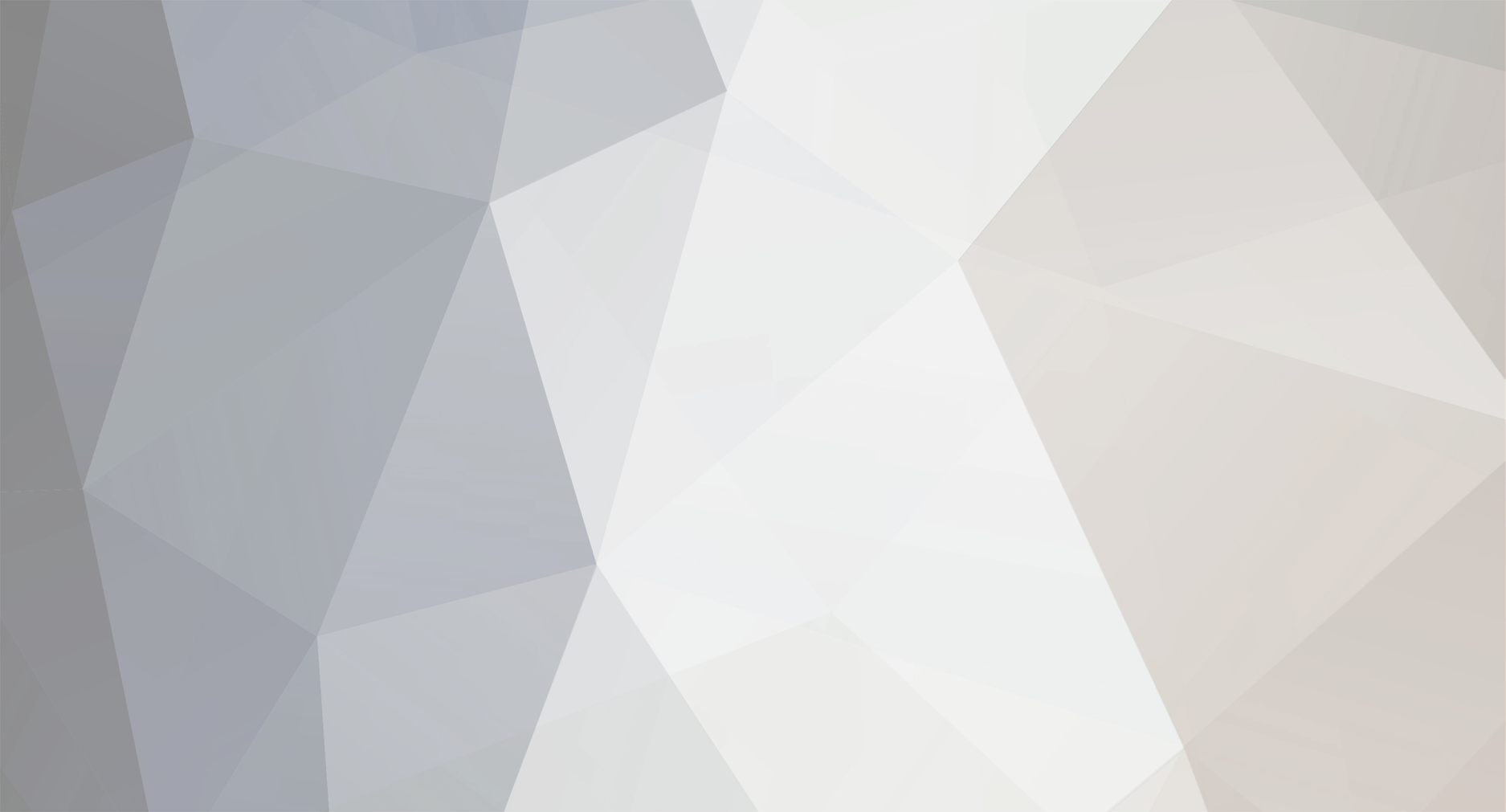
simmconn
Returning Member-
Posts
162 -
Joined
-
Last visited
-
Days Won
2
Content Type
Profiles
Forums
Events
Everything posted by simmconn
-
Building an energizer almost from scratch - advice on clamping zeners
simmconn replied to bobkatz's topic in Do It Yourself
Here is the impedance plot (phase and magnitude) of the transformer in an SRD-7SB with the SB circuit disconnected. Three sweeps were run with 1V input, output open; 1V and 2V input, driving a Stax SR-404 with its bias supplied externally. Take an educated guess, which curve is from which test condition? -
Output Stage Current Requirements for Electrostatic Headphone Amps
simmconn replied to JimL's topic in Do It Yourself
I see a few problems in your calculations. First, the load impedance is the characteristic of the phones, which is listed in your headphone’s spec sheet. It is not determined by the output voltage or current capabilities of an amp, which on the other hand are the amp’s design choices. Second, the reflected impedance to the amp is affected by many factors (and follows square of the turns ratio in an ideal case). In this case, the parasitics can have a significant effect on the load impedance the amp sees. Take a measurement and you may be surprised. Third, impedance is a vector. Using a scalar value is convenient but let’s not forget its vector nature and mostly reactive for the estat phones. The 1W of driving power would then be apparent power and not real power. Last but not least, may I suggest that we limit questions and comments regarding one project to a single or a couple of threads only? -
Building an energizer almost from scratch - advice on clamping zeners
simmconn replied to bobkatz's topic in Do It Yourself
That's all good statements in theory. My suggestion would be to plug-in the real-world numbers, do the math and find out what kind of voltage you really need/can afford, and go from there. For the protecting scheme, too. You now have a high voltage DC supply which can conveniently verify the protecting threshold of the candidate device. You could also connect the protection device/series resistor(s) to your phones and listen to them at comfortable levels. If you can't hear a difference, or even prefer the sound with the protection device present, viola! you've got a solution. FWIW, I found an MOV which looks like a 2W+ metal film resistor in my old Stax Lamba (normal bias). I guess at the time the non-linearity it brings was the lesser evil compared to a burnt driver. -
Building an energizer almost from scratch - advice on clamping zeners
simmconn replied to bobkatz's topic in Do It Yourself
An ideal shunt-type protection device for the estate phones should have: 1) Low (<10pf) and constant capacitance vs voltage and vs frequency - that pretty much crossed out all the silicon junction devices. 2) An I/V curve with a sharp corner, near-zero leakage within the operating voltage and well-controlled clamping voltage - that rules out most MOV devices 3) Fast acting. That excludes the gas-discharge type. What do we have left? Why use a shunt-type protector, just to give the amp and the transformer a jolt like a dead short when they are outputting close to their max voltage? The Stax transformer box adds a PTC in series with the transformer primary to mitigate this issue - and you know how people hated it. IMHO a better protection is to limit the output voltage of the amp. If the power rail voltage is limited, the amp's output is limited and the transformer's output is limited as well. -
Building an energizer almost from scratch - advice on clamping zeners
simmconn replied to bobkatz's topic in Do It Yourself
@bobkatzIMHO you are not likely going to get better performance with the TPA3116d2 class-D amp. It will have high noise and distortion than the amp modules in EHA5, plus the ultrasonic switching noise that may cause further intermodulation junk down the chain. Most if not all the imperfections you see in the measurement are caused by the transformer, such as higher THD at lower frequencies, the resonance at ultrasonic frequency that manifest itself as poor square wave response, plus other issues like phase shift (group delay distortion) that is not reflected in your tests. The transformer is the weakest link here, within the capability of the amp modules. Using a better transformer such as lundahl would help. I'm not sure if you can find one with turns ratio as high as 50. If not, you might want to switch to an amp with higher output voltage, if you need to maintain the 700Vrms output level. -
That's a common misconception about differential signals from signal integrity point of view. No output driver works out of vacuum. They are all power and ground referenced. Even with transformer isolation, there is imbalance in the windings and capacitive coupling between the primary and secondary, from windings to the core. In a practical world nothing is ideal. The AES diagram clearly shows how the current 'I' could create a noise voltage drop between the input shield point and the star ground point, which adds to the input signal in a common mode fashion. That's why there is a note in the end that says, 'as close as possible to each other'. How about at one single spot, can you get closer than that? Personally I wouldn't want to inject any dirty stuff from the ground of the source to IN- of my amp. So if I find out an RCA female to XLR male adapter connecting pin 3 to RCA signal ground while keeping pin 1 floating, I'd want to modify it.
-
Hmm, I wonder what kind of noise and hum level would be when you connect like that. Unless your source is true balanced pro gear with transformer-isolated output, most DACs and preamps have ground-referenced output stage. In other word, the +/- are not using each other as the return path, but pin 1 in that XLR cable. Once you include the PE connection and the signal ground connection in your common-mode return path, noise and hum inevitably gets included in the signal coming to the amp. Remember any amp has a finite common-mode rejection. However the theory says, I guess at the end of the day, whatever works best in my/your system matters the most.
-
I’m just saying, connecting like you described may not have the best hum rejection, and if we need to connect the PE and signal ground again at the amp chassis XLR input for better hum rejection, it defeats the purpose of running two grounds separately. That’s why I was asking if you have any measurement data to support your ground wiring scheme.
-
Ideally the PE connection doesn’t carry any supply current and is separate from the PSU return wire. However in the DIY T2 case, they are connected together in the PSU already. If you connect them again at the amp chassis XLR input (the amp PCB has a ground lug for that), it defeats the purpose of running them separately. Unlike connecting independently powered devices shown in your diagram, the T2 amp circuit is powered by the T2 PSU. So unless you have measured data to prove otherwise, I think using the PSU ground return wire(s) to the amp to double as PE should be sufficient. In my personal experience with DIY T2, the ground wiring is not a significant contributor to hum.
-
@jokerman777If the length of the spigot on the PPS washer gets close to, or is longer than the combined thickness of the TO220 tab and ceramic insulator, the hole on the L bracket must be large enough to let in the excess length. Otherwise the PPS washer would be crushed when you tighten the screw. Too bad you can’t do threaded holes on the L bracket for the same reason, and have to use the nut - split washer - flat washer combo which is a pain in the neck to work with when servicing the unit.
-
I agree that metal chassis should connect to the earth ground from the power cord/line input module. In general, I also connect the transformer electrostatic shield ground and the DC power supply ground (which is electrically connected to the amplifier's signal ground) to the chassis/earth ground. That seems to give me the lowest measured hum level. Sometimes grounding the input signal ground at the connector entry point to the chassis works best for me, but YMMV. In terms of DIY T2, since its in two separate chassis, the only way to ground the amp chassis is through the power supply ground wires in the umbilical cords. The center standoff near the back on the PSU board becomes the most convenient star-ground point. The wires going to the grounding point should be as short as possible and stay clear of the transformer leakage flux. Unfortunately that's not easy to do in the DIY T2 PSU chassis.
-
Both the 2SA1967 and the lessor 2SA1831 can still be had for less than $1 a piece, if you know where to look. They have the same B-C-E pin order so should be a drop-in replacement for the B832 (please don't take my word for it, verify yourself!). But I agree with you, it'd be better to save up for a better amp. On the Topping/transformer topic, I know people don't like the SRD-7SB because the transformers are taxed to provide the bias. Has anyone compared the SRD-7 and SRD-7SB with the bias circuit disconnected? I mean, does the additional bias tap on the SRD-7SB transformers hurt the performance even if not used?
-
Happy birthday, Kerry!🎂
-
The solder type is a lifesaver for DIYers, unless you want to deal with the uber-expensive crimper, the crimping dies, and the go/no go gauges. Having said that, I found the power rails considerably cleaner at the PSU board than at the amp board.
-
and now for something completely different part 3
simmconn replied to kevin gilmore's topic in Do It Yourself
Is it the 'ok bias' channel in your schematic that has large output offset with servo disabled? I gave my analysis in my post. Q24 and Q25 form a current mirror. The current through R21 should be the same as the current thru R31 and thru the R26. Apparently it's not the case based on your measurement. I would focus on the related few components. -
The protector board needs a solid ground, i.e. split +/-15V power with their common GND tied to the amp GND. A single floating 30V would not work, because the 12V relay only draws power from the +12V and will throw the GND off center and causes feedback to the comparators. You can share the +/-30v with the amp. Make sure the variety of 7812/7912 you use are rated for 35V or more, and the 7812 has sufficient heat sink for continued operation of the relay.
-
and now for something completely different part 3
simmconn replied to kevin gilmore's topic in Do It Yourself
@SatyrnineWhat does it mean by the minus sign on the voltages? It wouldn’t make sense unless you mark which pin had the red probe on it and which one had the black one. You might instead mark the actual polarities, like the pin with higher voltage with a (+). For voltage to ground such as the servo output, it should be the actual voltage. You marked -10V on the schematic but said 10V in the post, which one is true? Based on the voltage drops on R19/R21, it should be 10V, so the lower current mirror should have more current than the upper one. But that’s not the case when you compare the voltage drops across R25 and R31. So something must be off there. The transistors seem very mismatched. Btw, most of the reference designators are hardly legible on your hand-marked schematic. If you expect people to help you, at least make it easy for them to do so. -
You are welcome. It depends on how quickly they drift. My understanding is that the largest part of the drift is caused by the transistor parameters’ temperature effect. That also includes the Hfe of Q32 Q33. Unlike the balance servo, the offset servo is a proportional regulator so its error varies with the gain. Hence the offset varies with temperature. If it drifts up and down faster than like one hertz, it gets into the 1/f noise territory and needs attention.
-
That’s a good point. My understanding is that imbalance always exists in the circuit, and it’s meaningful to see if the imbalance is small enough for the servo to compensate. So it’s probably still useful to have the servo in the loop when troubleshooting, rather than trying to balance the circuit manually and then engage the servo. The servo opamp output is an indicator of the imbalance. I’d adjust the +/- active batteries in the opposite directions after warming up, such that the servo opamp outputs are well within the +/- power rails.
-
Good to know that the R ch works okay now. How high a voltage is too high on C/D? If it’s like the L ch before (about 1V). It’s normal for T2. If you want absolute zero offset, I have a solution in my post last Friday here.
-
I’m not sure if you used the “original” DIY T2 enclosure. The transistor mounting hardware are difficult to access in the recessed space and easy to get lost. I would do sufficient measurements to narrow down to a suspect before removing anything. Like you’ve found out, it’s not always the transistors that go bad. If I were you, I would measure the voltage drops on the resistors I mentioned in my post to see the current before removing any transistors from the heat sink. One lesser issue is the Vgs measurement you marked on the schematic, why some J79s have 0.5 to 0.6V and others have 1.5 to 1.7V? It’s still within spec but could be rearranged for better matching between the +/- arms. The T2 is not that complex, when troubleshooting you just need to trust the data and analysis more than your instinct and luck.
-
We are getting close. Now there are two problems. First is that R(D) doesn’t follow R(O-) at a 1:10 ratio. It’s a simple resistor divider by R90/R91. You may have a short or wrong resistor value in that area. Measure the resistance when powered off and you should find something. Second problem is that with matched (-) voltages at R ch active batteries, Q24 and Q25 are off by about 4V. It’s getting close to explaining the 50V imbalance we see at the output. Either Q26/Q27 has large mismatch, or they work under mismatched currents from Q28/Q29. By measuring voltage drops across R50/R51 and R54/R55 you should be able to get some clues. Note that sometimes high voltage transistors can “walk wounded”, having a minor leakage but not bad enough to burst into flames. L ch is working mostly okay. Don’t worry about the 10~15V offset or if it drifts over long period of time, as long as it is still balanced. We can come back to it later. Your Q24 and Q25 shows large differences in their G-S voltages. You might want to pay attention to that.
-
@demonkuro Sorry to be blunt, but people here who help you have their way of troubleshooting issues. To get the most out of their expertise, please do the measurement they asked so they can better help you. Extra measurement may help, as long as they are well documented. For instance, are the voltages marked on you schematic from the R channel? Also, doing shotgun-style component replacement without narrowing down to a suspect is rarely effective. Apparently the problem on the right channel is a balance issue. The final stage offset servo is most likely working fine. That's why replacing Q30 thru Q33 didn't help. Measuring Hfe of the transistors in circuit would not give you accurate results, especially when the base and collector are shorted together in the circuit. Assuming the voltages marked on you schematic are from the R channel. They look reasonable. There is one volt difference between the cathode of the EL34s (457V-456V). The triode-connected EL34 has a mu of about 10. For a matched pair under the same current, 1V of difference should create about 10V of difference between their anodes. But now there are 50V. That could be caused by different currents from the CCS. Measure the voltage drop on R18 thru R20, R17 and R14, and you'll get an idea how much current is flowing through the CCS. Do the same on the other arm and compare. To check the operation of the balance servo opamp that seems stuck, I suggested that you 'Follow the trace from O+/O- all the way to IN+/IN- of the opamp and see where the problem is.' I didn't see any feedback from you. Now that O+/O- differ by 50V, points C and D should be 5V apart, IN+/IN- of the opamp should be clamped by the diodes to approx 0.6V in the correct polarity, and both opamps should output close to rail after a few seconds. If you don't get the correct IN+/IN- voltage, you may have a short or a diode installed in a wrong orientation. If you do get the correct IN+/IN- voltage but the opamp still outputs zero, you may have a bad chip or a leaky cap (0.47u). BTW, film caps (polypropylene) are recommended over ceramics in those locations for lower leakage. It's a pain in the butt to remove the C3381s, but quite easy to check if they work correctly in circuit. They are used as current mirrors. Current that flows thru R86 should be roughly the same as the current that flows thru R84. Measure the voltage drops and you'll have an idea. Remember that I asked you to measure the top and bottom voltages of both active batteries of both channels? That would tell us if the imbalance is from the front-end or back-end. In other word whether the imbalance is before or after the active batteries. Before the balance issue is resolved, it's probably not necessary to repeat the hour-long tests. A better way is to take as many points of measurement as you need in one shot, shut off the power, analyze the data and go from there.
-
You would need to keep the associativity in your notes, i.e. which op amp controls which arm (+/-) of the channel, and keep note of the top and bottom voltages of both active batteries of both channels. It looks like the left channel's offset and balance are in check when cold, but drifts more than it should when warmed up. If none of the components in that channel are overly sensitive to temperature changes, chances are some transistors may not have good thermal contact to the heatsink. An IR thermal camera would be a great tool for troubleshooting that kind of problem. For the right channel, it looks like opamp 1 is not doing much to pull the balance back. You might want to check if it is behaving correctly. Follow the trace from O+/O- all the way to IN+/IN- of the opamp and see where the problem is. Note that the balance servo takes a few seconds to settle down. So the cold measurement can be done like 1 minute after HV turns on.
-
The offset of the output stage is maintained by the Q33-Q32 servo and they'll fight against any adjustment you make on the active batteries in the attempt to bring down the offset. My preferred solution (which may not be popular here) is to change R73 (6.2k) to a 10k multi-turn trimmer so that offset and balance adjustments can be de-coupled. In terms of balance, the balance servo around the LF353 has a relatively narrow compliance range. If you did not pay great attentions to the parts matching between the +/- arms of a channel, especially the triode-to-triode matching in the 6DJ8 tubes, chances are the LF353 opamps could bottom out trying to balance. Check the output voltage of the U7 and U8 opamps. The difference between them tells us how unmatched the two arms are. If any of them gets close to the rail (>10V or <-9V) I'd want to intervene. Adjusting the two active batteries' voltages in the same channel in opposite directions can bring the balance servo back to their comfort zone. Swapping the 6DJ8 tubes may also help, if one has better matched triodes than the other. Mismatching is not always a bad thing - slight mismatch adds some 2nd order harmonic which is pleasing to the ear. 740V on the active battery is a starting point/nominal, you may end up a couple of volts away from the nominal which would be fine.