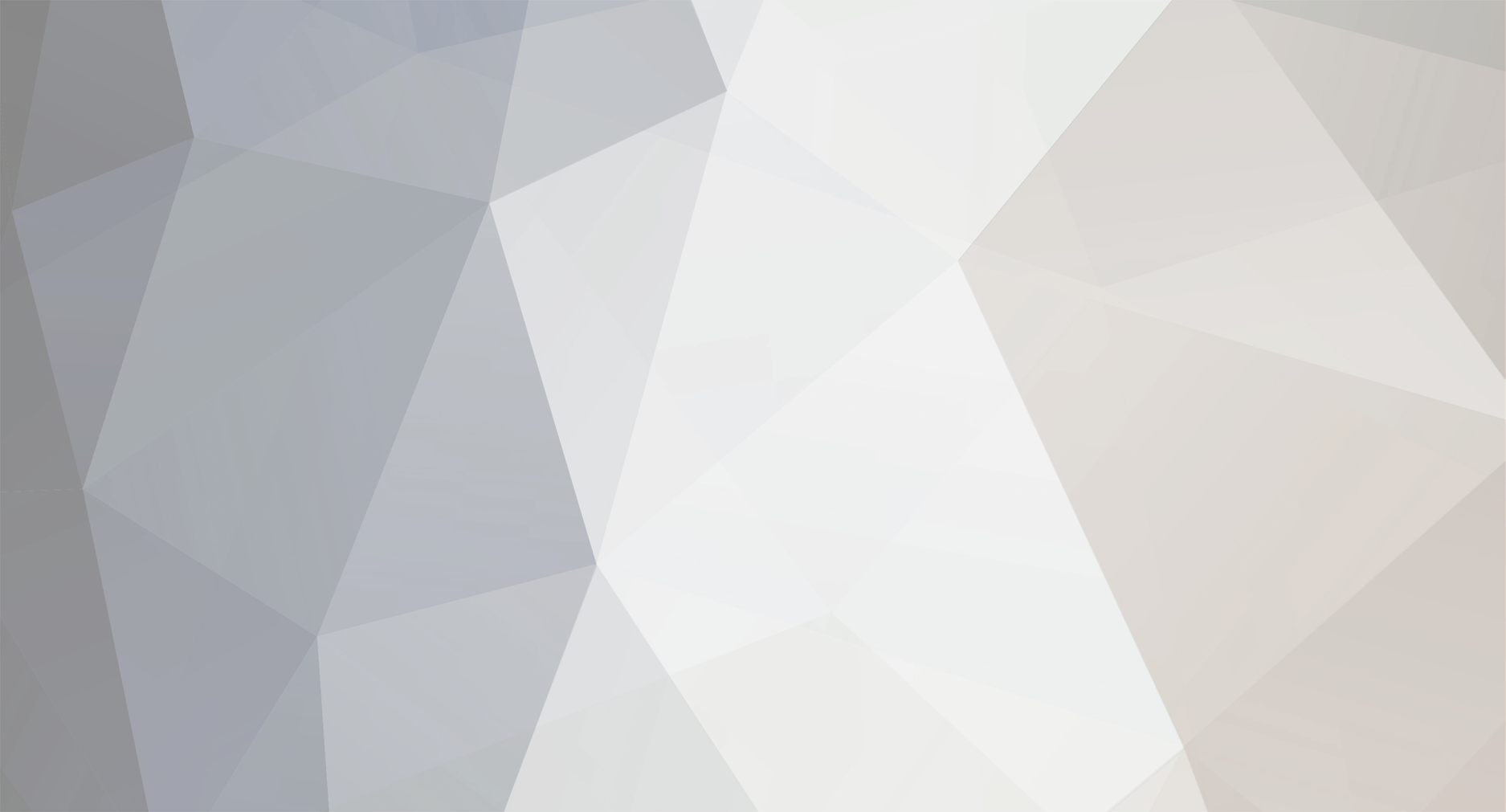
simmconn
Returning Member-
Posts
161 -
Joined
-
Last visited
-
Days Won
2
Content Type
Profiles
Forums
Events
Everything posted by simmconn
-
I’ve been using the DN2540 in TO-92 package since my first Carbon build without any problems on the amp board. However I’ve seen two instances where the DN2540 on the GRHV developed a Drain-to-gate leakage. That caused excess current thru the HV PNP. In one case (my own build) it was caught in time and didn’t do any real damage, in the other case (someone else’s board with a TO220 DN2540) the PCB was cooked, the ST9360 failed and brought down both the BC557s. The leakage problem is regardless of the DN2540 package. I’m suspecting in the cascode CCS there may be a corner case where it is stressed beyond the safe limit.
-
The GRHV is not particularly fault-tolerant. If any of the high-voltage part had a breakdown, it will likely cause a chain reaction and bring down other parts, including the expensive (if you didn’t buy from AliExpress) LT1021. So being able to test the breakdown voltage of the parts before putting them on the board helps a lot.
-
It would probably work, but I wouldn't call it a 'good' replacement. You would have to deal with a different package, higher Cob and lower Hfe. In theory any NPN with sufficient breakdown voltage can be used in that position, but since it is the only gain stage in the regulator (both the STN9360 and the SiC FET are followers) and consumes very little power, I tend to use lower current parts with potentially higher Hfe. The compensation cap value was designed for the KSC5026M, so if the replacement part has lower Cob, increasing that cap may be necessary for the stability of the circuit.
-
What’s the purpose of the 555? It seems that it’s not doing much meaningful. Even if you want to keep it, at least its pin 3 and pin 7 output opposite polarities such that you won’t need another inverting stage outside…
-
Thank you, and big thanks to @kevin gilmore@Kerry and many others who made this DIY journey really enjoyable!
-
Thanks! I've got to bump this thread to page one with some real stuff 😀. The GGPT (Grounded-Grid Pentode/Tetrode) now gets a proper PCB laid out: I made a few deviations to the common choice of parts: 1) I found some 2SK332, could be Sanyo's answer to the low noise dual N-JFET market back in the day. They cost me about 60 cents a pop, so I ditched the LSK389. The footprint is also usable for a pair of 2SK170s. SOT-23 footprints are added for the 2SK209, and a few others that share the same pinout. 2) Through-holes on the SMD pad for the SOT223s are a big no-no for machine assembly due to solder wicking, but works okay for hand soldering. It allows the use of A970/C2240s. I found some from a Chinese manufacturer Foshan Blue Rocket Electronics, pretty decent build quality, good low-current linearity, and cheap (14 cents a pair). 3) All through-hole RCs. I know the world has moved to SMD but I have quite some through-hole resistors accumulated over the years, and personally prefer leaded components on tube PCBs due to the thermal and mechanical stress they have to endure. The FU50 tube sockets are so big and everything else have to dance around them. I chose not to use slotted pads at the exact socket pin locations, instead having soldering pads on the side allows flexible or semi-rigid connections from PCB to the tube socket contacts, which can absorb the strains. The scheme is similar to what Stax had on the original T2 PCB. A couple more mounting holes are added to allow other types of tube sockets to be used. The board mounting holes have the same distance compared to the Carbon board. This board can overlay on top of the Carbon board in the chassis where I have enough Z space left. They can share the heat sink and the power supplies. The goal is to be able to switch between them with a flip of a switch. The GG Pentode with GU-50s and the GG Tetrode with 807s, side by side: The 807s have slightly better measured performance, at the voltage level that I probably never going to drive my phones at (when I'm wearing them).
- 14 replies
-
- 12
-
-
The so-called 'active battery' is a shunt regulator IMHO. I would recommend that you simulate any circuit changes for performance (shunt impedance) and stability. The original circuit does not seem to have enough phase margin and can use some compensation. My calculation shows either adding a 1.2pf cap across the two 820k feedback resistors, or increasing the shunt capacitance to 0.1uF would help. They each have their pros and cons. The calculated capacitance is so small that parasitics can throw the circuit in either way and make it 'touchy'. Using 2.2nF compensation cap would significantly increase the loop gain in the mid- to high-audio frequency range and reduce the output impedance as you have observed, but also make the stability worse. Since the active battery is part of the signal chain, I would rather shoot for flat impedance across the audio range and as small phase shift (group delay) as possible. I'm not sure what your test gig looks like. It would be important to test it with a source impedance similar to the real circuit. My sim tells me that the original circuit when properly compensated can be pretty flat within 20KHz and has -3dB point over 200KHz. On the other hand, the LT1021 due to its high-ish operating current requirement, does not necessarily bring much gain to the overall performance of the active battery compared to the LED strings.
-
Ah, okay. Sorry I misunderstood the question. It’s certainly possible, but usually the two CCS blobs are physically away from each other. IMHO given the other potential component mismatches, sharing the same LED string may not make a big difference in the current matching between the CCS.
-
My take is that 2 LEDs in the string allows a higher emitter resistor value and therefore better local NFB. Sim shows that the effective impedance of the CCS roughly doubles with 2 LEDs vs 1. That come at a cost of reduced voltage compliance range and slightly increased power consumption. They are not a big deal for high voltage CCS, though.
-
Although the KGST uses the same front-end as BH and Carbon, its simplicity comes at a cost. In the 'stock' form, the open loop gain is about 78dB and closed loop gain about 59dB. Having only moderate global NFB means that the circuit has to have a wider open loop bandwidth and good linearity to begin with. It also suggests that the measured performance would depend a lot on the matching and inherent linearity of the tubes. Below is the THD+N vs amplitude plot I did earlier on the 'stock' circuit. The max output is about 200V. It kind of falls short for an amp with ±400V supply. With the experience from the pentode experiment on Carbon, I tried a few pentodes and tetrodes with the 'stock' circuit. The first one I tried was the 6973. Why 6973? Because it's pinout is very close to the 6S4A, such that I didn't even need to cut any PCB trace in order to use it. The result was quite ok. The max output went up to 500V and the lowest THD reduced by about a half. Knowing how much the 6973 costs on ebay I think I should have a better use for them 😉 Then I tried a few others, including the 832A. It has one of the cutest bottles and yet is not that expensive. I was eyeing on the Breeze audio 832A SE amp enclosure. The box may look hideous to some people, it would be really cool to have a unique eStat amp like that - if still offers reasonably good performance. The 832A didn't pan out very well. The THD flattened out at 0.01%-ish, mostly 2nd harmonic, due to the mismatch between the two tetrode sections. Some people may appreciate the 'tuby' sound, I decided to move on. I looked for a triode with amplification factor of 30 (twice that of the 6S4A), which also allows 400V DC on the plate (800V peak). It's not that easy to find real triodes like that, unless I go with the exotics such as the 801-A/10Y. I heard about the 12HL7/12HG7/12GN7 family. The video output pentodes designed for the color TVs in the late 1960's. They allow 400V on the plate, have a mu of 30 to 50 when triode-strapped, and said to have great linearity. Below curve was captured with one of them at X=100V/div, Y=5mA/Div, Vg1= 2V/step It turns out (again) it's not easy to find well-matched pairs because the curves in the high voltage region vary a lot from tube to tube, and the g2 power would be over spec when triode strapped idling at about 400V. I did get some nice distortion plots when they are wired in pentode mode (below FFT with 12HL7 at 100Vrms output). Unfortunately not all of them are happy with 800V peak on the plate, although 400VDC is okay on paper. So I came back to the drawing board, trying to make it work with the 6S4A. In the 'stock' circuit, the limiting factor to the output swing is the signal amplitude at the 6S4A grids. Adjusting the ratio between the 200K/6.8K resistors on the active loading NPN pair can increase the idling voltage and improve the max swing into the 6S4A. The downside is that the output impedance of the driver stage will increase, and the open loop bandwidth drops a bit due to the Miller caps on the 6S4A. Also I don't need the full 60dB gain. '200mV sensitivity for rated output' was established from the analog-era when tuners and tape decks are the most popular sources, not to mention 100mV for rated output. Doubling the resistors at the source of the input JFET aught to do it. The end result is extended output swing: And a not super clean, but still okay output FFT spectrum at 100Vrms. Well, that seems to be the best I can do. I'd live with(in) its limitations, close the lid and enjoy the music!
-
I took the challenge again to squeeze a DIY eStat amp into a small enclosure. This time is a KGST in a Breeze Audio 2409. I was using an Antek AS-1T350 with a separate low-profile quasi-toriod for the LV supply. The Antek was well shielded with both copper and steel bands under the wrapping, I still need to move it all the way back to reduce the hum. I'm glad I pulled the trigger and ordered the custom R-core transformer. I asked the vendor to build two identical bobbins to balance the flux, each with a 115V primary, a 350V, a 17V and a 6.3V secondaries. With the copper band on the outside, the flux leakage is so low that I couldn't pick up anything significant at 60Hz or 120Hz on the FFT. I have more than twenty 6S4 and 6S4As, many of which are NOS. However I had a hard time matching a second pair, and had to decide between a well matched pair that is slight noisy and one that's less well matched. The curves look all similar below 400V, but could go all over the place on the higher voltage region. The below picture is kind of an extreme case, an example that two tubes both testing good on a tube tester at 150V on the plate, may be quite different when you need them to swing up to 800V: <To be continued..>
-
You’ll need some kind of +/-15V power supply, GRLV being an option. There are left and right versions of the GRHV board, one with the bias supply and the other with the 7815/7915 LV supply. The sellers from China cut the corner and only produce the GRHV board with the bias supply. You’ll end up receiving two of those, and still need the LV supply.
-
The pentode experiment gets a little twist - with a beam tetrode. In my search for an acceptable output device, I went through the popular low-power transmitting tubes. The 807/6L6 family has such a wide, kinky curve in the low current region with typical Vg2 (250V) and was rejected as a candidate at the first glance. However, the curves around zero Vg1 looks quite linear. Lowering the Vg2 could sort of 'bring them down' to the low current region. With about 60V on the G2, the kinks are largely gone, and the linearity looks pretty good (pictured below X= 100V/div, Y= 5mA/div, Vg1= 0.5V/step). Another benefit is that Ig2 comes down considerably with such a low Vg2, which allows me to use the same simple G2 supply used with the GU-50 (zener diode paralleled with a 10uF cap). I compared quite a few tubes on the curve tracer. The National Union 807s (shown above) from WWII era seem to have the best linearity and are the most stable. The RCA and Sylvania tend to oscillate on my test jig. 1625s are about the same. Unfortunately I don't have enough National Union for a matched quad. The earlier 6L6/6L6-G are not officially rated for 400V plate voltage and have to be excluded. The Tung-sol 6L6WGB/5881 (the real deal, not the 'reissue') looks much more linear compared to the 6L6GC. The Sylvania 5881 (shown above) although has the same internal structure as the Tung-sol, doesn't seem to be as linear. The 1624 would be an interesting direct-heating variant that has a bit higher gain than the 807. The 2E26/2E24 brothers are suitable, too. Here are the 807s on the test bed: The result is convincing: The 100Vrms output FFT shows harmonics -115dB below the fundamental: The 1624 turned out to be a disaster. It was hard to get a clean, low capacitance filament supply. When attached to the signal path, the common-mode noise would kill the S/N and the capacitance would mess up the frequency response and THD. I have to admit I don't have much experience with direct-heating tubes in circuits where every uV counts. It would be nice if the few exotic direct-heating tube eStat amp owners can get their units measured and share their secret to success... The grounded-grid cascode output stage is such a nice thing that it allows us to play with many tube types, as long as they have enough plate voltage and power ratings and are reasonably linear. We could end up having unique amps that still have top-notch performance.
-
As planned, the other channel is modified the similar way but with GU-50 tubes as the output device. The performance is comparable to the SiC FET: The distortion profile at 100Vrms output is pretty good, too, with all harmonics -115dB below fundamental. It turns out, the ESL speakers require considerably more voltage than 1KVrms. My Martin Logan CLS-II transformers have about 1:160 step-up ratio at the low end, gradually tapered down at the high frequencies - so some EQ is also needed for a direct-drive amp. The Quad ESL-63 is said to have 1:260 step-up ratio. 1KV is probably just going to make it to a BGM sound level...
-
hmm, perhaps someone has the habit of populating all the parts first, and then finish up all the soldering joints. Easy to miss a thing or two when there is no AOI. After all it’s only the servo…
-
Share your favorite stores and parts here.
simmconn replied to omendelovitz's topic in Do It Yourself
The local surplus store is closing its doors next month. To not let the 2SC3381s go into a black hole, I’m running a group buy. Mixed GR and BL grades, $0.5 each with minimum of 10 pcs. Shipped from California. PM me if interested. Also available 2SC3067 dual NPN at the same price. Sorry no JFETs or high voltage transistors. Group buy closes Friday 6/24. There is a chance someone may scoop them up before I do, in which case refund will be issued. Please don’t blame me if that happens. -
Based on your first question you should probably stick with the original design. The 24V zener diode protects the MOSFET from excessive Vgs during power up, when the output capacitor is charged up from zero. Since you recognized the CCS, I probably don’t have to elaborate the benefit of a CCS vs a resistor. The simple answer is yes, you can replace the CCS with a resistor with reduced performance. The 10M90S is in short supply, at least from the US distributors. You can replace it with IXTP01N100D, or based on your rectified DC voltage, try a DN2450 or DN2470. The 1.2k resistor would need to be adjusted to obtain the same current through the zener diode chain as with the 10M90S.
-
Thanks. A fixed-setting current limiter before the passing device would also help the SOA issue. I can also do something like the following: With carefully selected R5 and R8 values, M1 and U4 can split the start up VIN. A resistor can be added to the M1 source so it also acts as a current limiter during normal operation. After all, most of the high voltage Si-MOSFET and SiC FET are designed for switching applications. We need to tread carefully when using them in linear mode.
-
The second part of the experiment is the PSU. The Circlotron HV power supply (goldenreferencehv900new.pdf) uses an ingenious way to overcome the component voltage rating limitations, by using a floating reference point at 1/2 of the output. Since I'm not pursuing 900V, maybe I can get away with replacing a few parts in the GRHV and settle at 800V? Aside from doubling up on the input and output caps, the STN9360 needs to be replaced with 2SA1968, and KSC5026 replaced with 2SC3675 or 2SC4686A, and the resistor divider updated. Done, I thought. After a couple of minor volcano eruptions, I had to go back to the drawing board. Since they both failed at power up, it looks like either the current limiter didn't work, or it was overwhelmed because the SiC-FET had a D-G breakdown. I put the SOAs of the SiC-FET side by side, comparing their allowed VDS under 0.1A of current at 25C, which is the PSU start up condition: Apparently the C2M1000170D is the most robust, allowing 700V (100ms). The G2R1000MT17D scores the second, allowing about 450V. The MSC750SMA170B only allows a little above 300V. Considering it's specified at max Tj, the 25C spec should be better. So what works for the C2M1000170D may not work for the cheaper subs. It could be SOA violations that killed the SiC FETs. The GRHV soft start uses the cascode CCS to charge the Tantalum cap until the SiC FET VGS is higher than its threshold voltage. The SiC FET turns on slowly so the current limiter has plenty of time to get in action. The output cap is then charged with 0.1A of current over a few seconds until the preset output voltage is reached. The above assumes that the PNP is ON at the beginning, which is not exactly the case. The output cap needs to be 'pre-charged' to about 1.2V to establish a DC path for the PNP to turn on. The per-charging is done with the SiC FET fully on, and only the current limiter in effect, when the SiC FET is most vulnerable. Although the pre-charge time is short (several ms depending on the output cap), it's better safe than sorry. My solution is to add a diode D5 to establish an initial DC path for the PNP. I chose a low-capacitance small signal schottky diode, with a resistor R2 in series to further reduce the effect of its junction capacitance. Also during the soft start, the charging current increases quickly to reach the current limit, but the output voltage only ramps up linearly, which means the SiC FET would pass a lot of current when its VDS is still high. It would be great if the VDS can affect the current limit and set it lower during ramp up. So I added R5 and zener D7. D7 has a higher voltage than the normal working dropout voltage, so R5 wouldn't take effect during normal operation. After the above mods, the SiC FET has not failed. I also reduced the output voltage to 750V and reduced the input accordingly. The last failure happened a few minutes after turning on, and was caused by thermal runaway of the PNP. It turns out the DN2540 developed some kind of gate leakage, where the voltage drop on its source resistor no longer controls/represents the output current of the CCS. A lot more current gets dumped to the PNP, causing it to burn. I couldn't figure out what caused the damage, perhaps some transient conditions. So I added another zener diode D8 to protect the DN2540. Now both GRHV PSUs are upgraded to 750V output and work stably so far. The amp boards work okay when connected to the 750V PSU. Now is the time for some measurements. First is the all-JFET configuration. And swapping the SiC FET back in as the output device, with visible improvements: The SNR is about 6dB worse compared to the original Carbon under 400V PSU, due to the feedback resistor mod in order to get a higher output voltage. Did I get the 1kVrms output I was looking for? Yes. Well, sort of. The problem is, the volcano eruptions ruined two SiC FETs and I don't have any more to populate the other channel. Digi-key has the C2M1000170D back in stock now, but the price has gone up to nearly $10 a piece. I guess I'll keep using the GU-50s on the other channel.
-
I was going to name it 'Double the Carbon, double the voltage, double the fun', but I'm afraid that would be too wordy. Ever since I measured the output swing capability of the Carbon, I wanted to see if it can drive my ESL speakers. To do that, I'd need a beefed-up version that can output at least 1kVrms before clipping. That's 1414V peak, out of a ±750V to ±800V PSU. To simply scale up the Carbon amp and the GRHV PSU without major changes to the PCBs, a few hurdles would have to be overcome. First is the 900-V rated 10M90s in the cascode CCS that bottom out with ±450V PSU. When I was browsing the high voltage FETs at Mouser, I found the UnitedSiC UF3N170400B. It's a 1700V 6.8A SiC JFET, naturally in depletion mode, perfect for the upper device in the cascode CCS. The threshold is about 9V, which helps the DN2540 to get further into the constant current region yet keeps the power dissipation still in check (no heat sink needed even with the TO-92 package). The drawback is the package. The TO268-7 isn't too friendly for a DIY thermal solution. I had a few carrier boards made with aluminum-based PCB. According to simulation, the little board would give me 9 degree temperature difference from the package case to bottom of the board when the FET is dissipating 9W. I chose black solder mask, hoping to get a bit better heat radiation capability. 10 boards cost me about $3 at JLC. They also have copper-based PCB with a special process to have the base copper flush with the top surface for a much, much higher K. Too bad the NRE is about $150, so I chose the cheaper route with aluminum. The insulation is good to 3kV so this board can be bolted directly on the main heat sink without additional insulation. Isn't that great? The next bottleneck is the 600-V rated STN9360 when the PSU voltage reaches ±600V. I replaced them with the 900-V rated 2SA1968s. Thanks to the cautionary words from spritzer, I started cleaning up traces with high voltage differential that are getting too close to each other. I removed the middle pad 'A' in the 10M90s footprint, and re-wired a couple of traces on the back. With the bias changed from 24V to 13V above B-, the JFET can be used as the output device as well. At almost $10 a pop, they are considerably more expensive than the SiC MOSFET they are replacing. So the full-JFET configuration shown below is more of a proof-of-concept than anything else. The feedback dividers are changed from 200k:200 ohm to 440K:470 Ohm to maintain the gain and allow the output swing to double, without having the feedback current overtaking the idle current through the input JFET. Two 10pf 1KV caps are in series as a 5pf cap, since I don't have the proper 2kV rated caps. Not a great idea. I was lucky it didn't blow up. Technically the board is now ready for up to ±850V. I tested the SiC-JFET 'doubled carbon' config with ±400V PSU. The performance is slightly worse than the original Carbon. Is it worth the effort? We'll see. (To be continued...)
- 10 replies
-
- 13
-
-
@ibuski It looks like an used USSR-style socket. I would prefer that type of socket more than the NOS socket from China. I don't think the variations in design matter that much. As long as they were originally made for the military/industrial use, the quality should be trustworthy. @nopants The 10M90s still burn 7 to 9W each depending on the B+ voltage and the idle current. Using the enclosure side panel as heat sink should be doable, but it could get pretty hot. I would put some warning sign stickers on the chassis.
-
@ibuski Thanks! Speaking of low-cost FU50 sockets from China, there are different kinds. The socket on the left was removed from a NOS socket set with the cast aluminum frame. The frame helps the tube to align properly, and also works as a mechanical shield of some sort. It is unnecessary for a DIY amp IMHO. The ceramic socket base is pretty well made with good tolerance. The pin contacts have large flared openings and two holes on the soldering tab. The entire socket set including the aluminum frame can be had for about $3 each in the Chinese domestic market. The one on the right is the 'new production'. I got them for less than $1 a piece. Some with tin-plated contacts can be even cheaper. However the contact has a much smaller opening on the top, and a single oblong hole on the soldering tab. There is a risk of pins getting plugged into the well but outside the contact. The ceramic base are often poorly made with an uneven mounting surface. What's more, the pin 1 location is different from the NOS socket. Do not mix them! I would say go get the NOS socket set, spend a few minutes to remove the frame and end up with a socket in better quality. The socket mounting hole pattern is somewhat unique. A caliper and some middle-school trigonometry will be useful to figure out the exact angles of those mounting holes.
-
Since you are getting so close to the Paltauf and understand how the circuit works, why don’t you share with us the details? There is no problem for an unaffiliated user to disclose what he/she can see in plain sight, I assume. What I can see is that sharing is part of the core spirit of this site and what drew us together to begin with.
-
I'm finally able to put a closure on this pentode experiment, sorta. What finally improved the THD figure between 300V and 500Vrms output is the driver transistor. I replaced the PZTA42s with TTC004Bs when trying the original GG circuit with EL34s, while the PZTA42s remained in the left channel. With SiC FET as the output device, the driver transistor has a pretty steep load line, so the nonlinearities on the upper left portion of the curve didn't matter that much, as long as the idle Vce is chosen to be high enough to avoid that area. With the GU50 tube as output device, the driver transistors not only need to swing current, but also swing voltage (about 10Vpp), so the load line is more flat. The nonlinearities of the transistor becomes more problematic. The PZTA42s have to go. The KSC2690s I have on the left channel have higher hFE than the TTC004B on the right. The two channels ended up having very close THD+N curves. The 2nd harmonic is more prominent than the 3rd in the left channel with the KSC2690s, not sure if that's consequential. The hum is 110dB below the 100Vrms mark, with the 12.6V filament transformer CT simply tied to B-. I'm quite happy with the sound on my SR-009. It has the basic characteristics of the Carbon with a very slight touch of tube softness, yet not losing resolution or immediacy. I searched up and down but didn't find another pentode more suitable for this role, at least on paper. If some day I manage to put this into an enclosure, the ugly 'hats' would surely be sticking out.
-
Thank you, Dr. Gilmore. Given the background of amir (mid-high level on the corp ladder at M$), I wouldn't expect him to be as hands-on as the lab monkeys who spend most of their days with an AP. In an earlier post on that site I saw him struggling with setting up the AP to measure the deviation from RIAA of a phono pre-amp. Apparently he's never done that before and just like many of us, don't want to read the manual. Everyone has his/her limitations and comfort zones that takes some courage and effort to step out of. To give this guy some credit, he is able to measure the conventional gears in a consistent way, disclose the data and offer some objective comparisons/analysis, at no cost to everyone who is interested. That alone is worth some praise. Besides, some data is better than no data. When it comes to discrete R2R DAC, what intrigues me is that most designs use generic logic chips to drive the resistors. No matter how well the resistors are matched, the driver chips are not. No manufactures would specify or production-test the matching of a 10 cent bus driver, bit-to-bit or part-to-part. Parts coming from the same batch could be from the same wafer and perform somewhat close to each other, but there is no guarantee. The end result is therefore pretty much on a 'best of luck' basis.